YPS: Packaging that’s top of the class – even class 7

Supplier News
A manufacturer of rigid plastics for health & pharmaceutical applications has purchased a new packaging line, while ensuring their production facility meets all the ISO Class 7 cleanroom requirements.
The new line was supplied to the multinational producer by automated packaging specialists Yorkshire Packaging Systems (YPS), along with a full package of installation, commissioning, training and ongoing engineering support.
Glyn Johnson, MD of YPS, explained: YPS supply a wide range of automated packaging equipment, so we can find the ideal system for any production environment, matching a machine’s specification to our customers’ precise requirements.
The manufacturer was setting up a new production facility in the UK, moving production from overseas. Common in pharmaceutical and healthcare production, the new facility had to meet the stringent requirements of an ISO class 7 cleanroom, including requirements related to air flow, air quality and temperature & humidity control. The standard also specifies that equipment must be selected to help meet these requirements.

The new packaging line consists of a Pratika 56 MPE X l-sealer and double chamber shrink tunnel. This particular model of l-sealer is servo-driven with no requirement for compressed air, which is therefore helpful in meeting Class 7 requirements related to air flow control.
YPS were able to work with the manufacturer and host their team for demonstrations to fully understand the proposed equipment. Several other features of the machine particularly appealed to them, including the dual-access, perspex batwing doors which make it very accessible, easy to clean and easy to see, helping them to keep their cleanroom facility up to standard.
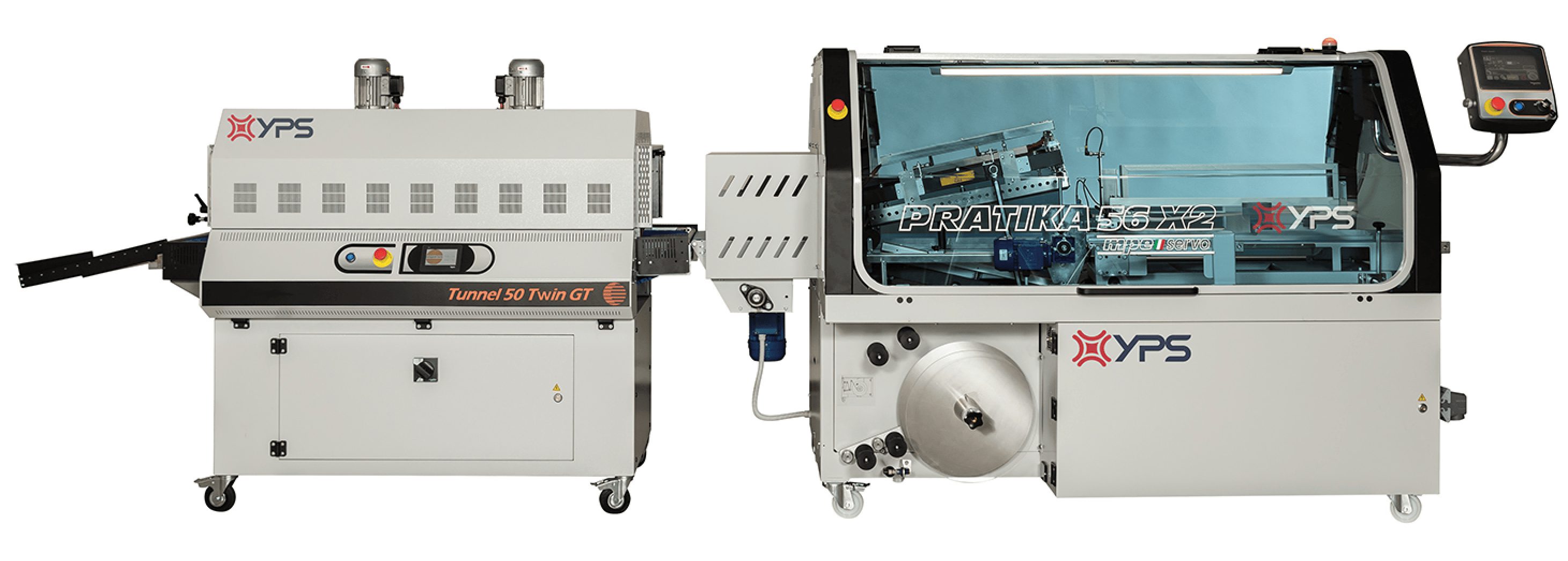
The company were also impressed by YPS’ engineering and support package following installation, delivered by YPS’ own dedicated and well-trained engineers.
Following tests that ensured optimum performance, the line has been running on the manufacturer’s previous film stocks. Further tests led by YPS are ongoing to select optimum new film options for the future.
Glyn commented: The manufacturer is known for its innovative approach, using leading technology to be ahead of its field. Their new packaging system had to meet both their class 7 requirements and their high general standards and we’ve been delighted that they’ve been so happy with the equipment and service that we’ve provided for them.
Related News
-
Supplier News
YPS: ROI of less than 12 months for automated ecommerce bagging equipment
-
Supplier News
98% recycled-content flexible film now available from YPS
-
Supplier News
YPS: Pack consistency improved whilst increasing production speed for pharmaceutical manufacturer
-
Supplier News
YPS announce commitment to net zero by 2035
-
Supplier News
YPS: End-to-end automated packaging system streamlines ecommerce operation