NPP: A guide to pallet wrap machine maintenance
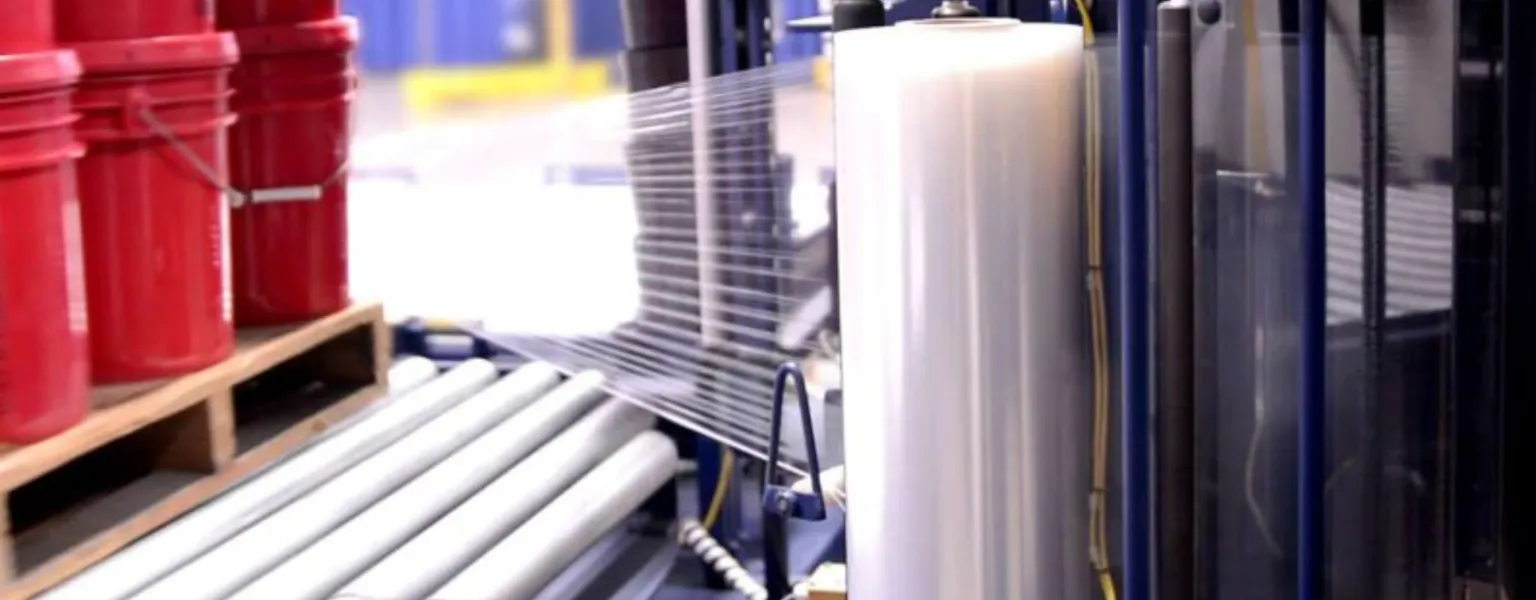
Supplier News
By Grainne Carroll
In busy warehouse environments, pallet wrapping machines are the backbone of the dispatch line, working tirelessly to keep operations efficient and goods secure.
Like all industrial equipment your pallet wrapper needs to be regularly serviced and maintained to minimise costly breakdowns, reduce material waste and unexpected downtime.

Why regular maintenance matters: Performance, safety & longevity
As a trusted partner of leading brands such as Atlanta Stretch, Lantech and Plasticband, we know that regular machine maintenance will help ensure your machinery performance.
With over 40 years industry experience we have seen the many benefits and advantages of implementing a regular maintenance plan and know it is an essential tool to keep your operations running smoothly.
Below we discuss these benefits in more detail, look at some common machine issues, and include a handy checklist to help you implement a maintenance plan tailored to your own operation.
Why does maintenance matter?
- Reduce downtime: regular maintenance will improve the reliability of machinery with fewer emergency breakdowns.
- Lower operational costs: a well-maintained machine uses the optimal amount of packaging materials and prevents the overuse of stretch film.
- Extend machine lifespan: regular maintenance can prevent many machine faults, extending the lifespan of your machinery and improving return on investment.
Common issues & how to prevent them
Preventative maintenance isn’t just about oiling a few gears. Here are some common issues we regularly see and the steps you can take to prevent them developing into problems.
- Stretch Film Problems: Tearing film or inconsistent wrapping? Check your pre-stretch rollers. Worn-out rollers not only affect wrap quality but also increase film usage.
- Debris and Dirt Build-Up: Bits of stretch wrap, pallet splinters, and general dust can collect under machines. This debris can jam moving parts and wrap around the drive system, leading to motor failure or blown fuses.
Tip: Establish a weekly cleaning routine using a vacuum or brush. Wipe down rollers and sensors to prevent grime buildup.
- Roller and Belt Wear: Drive belts, chains, support wheels—these moving parts wear out over time. Misalignment leads to inconsistent wrapping and product damage.
Tip: Have your engineer check roller alignment, tension levels, and belt condition at each service.
Your maintenance checklist:
We’ve put together a handy checklist to help plan and schedule your maintenance. Click here to download!
How often should I service my pallet wrapper?
Regular servicing by a certified engineer is another key component in optimising your machine reliability. At NPP our team of engineers work with companies throughout Ireland and the UK safeguarding their machine performance.
How often you service your machine will depend on usage, operating environment and machine type, but consider the following as guidelines when scheduling your service.
- Low Volume Use: <35 pallets per machine per day = 2 services per year
- Medium Volume Use: 35-70 pallets per machine per day = 3 services per year
- High Volume Use: 70+ pallets per machine per day = 4 services per year
Find out more about our Service Agreements.
Final thoughts
Routine maintenance isn’t just a nice-to-have, it’s a critical part of keeping your warehouse running efficiently. Whether you’re dealing with turntable machines or rotary ring stretch wrappers, staying on top of wear and tear protects your equipment and your bottom line.
This article was originally published by NPP: A Guide to Pallet Wrap Machine Maintenance
Related News
-
Supplier News
NPP: The benefits of automating your pallet wrapping process
-
Supplier News
NPP: Choosing the best pallet wrap machine for your business
-
Supplier News
NPP: Boneguard – Puncture resistant packaging
-
Supplier News
NPP: 5 ways case erectors can benefit your company
-
Supplier News
NPP celebrates its 40th anniversary