YPS: Unique conveyor system achieves accurate packing for lightweight products
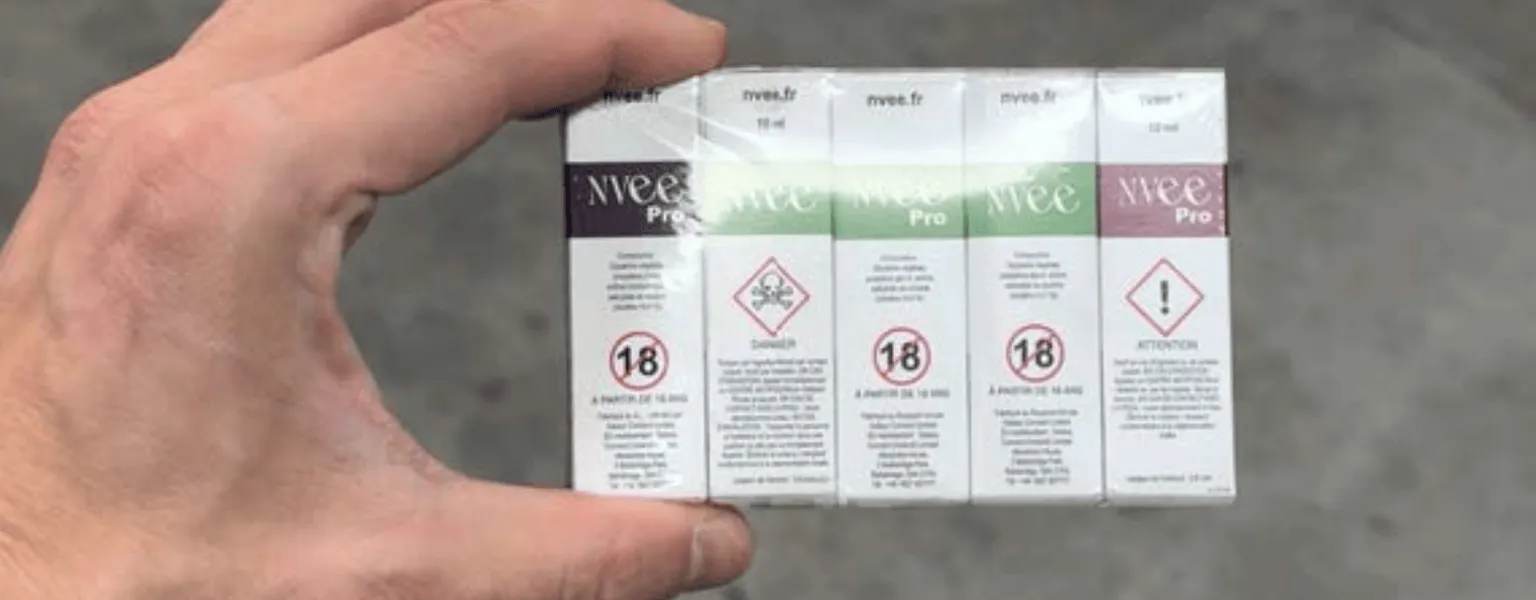
Supplier News
A three-belt conveyor system was recently specially designed by Yorkshire Packaging Systems (YPS) engineers to automate the shrink wrapping of small, lightweight e-cigarette packs.
An e-cigarette manufacturer approached YPS looking to completely automate the bundling process at the infeed of their packing process, to speed up production and reduce reliance on labour.
The system had to guarantee a neat seal every time, for varying product collations.
YPS supplied a fully automatic, servo-driven L-sealer to wrap the packs, but it was the infeed conveyor arrangement that was specially designed to provide the level of speed and accuracy required.
Three infeed conveyor belts were supplied, with individually controllable speeds. The first conveyor moved relatively slowly to allow a single operator to load the products in the correct rotation for shrink wrapping and the correct order for the desired collated packs.
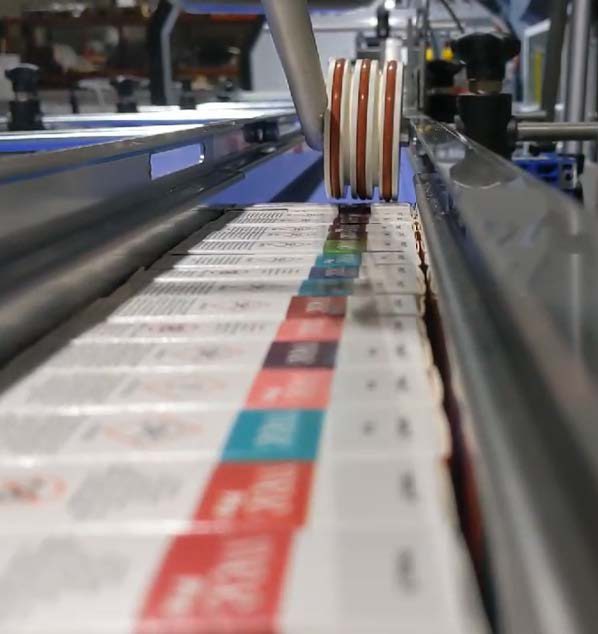
A sensor located on the second conveyor would read when the final conveyor was full, with no gapping between products. This sensor would then release the final conveyor to rotate by a programmed amount, related to the number of packs required for the current collation, and push them into the sealer for the bundle to be shrink wrapped.
Changing the line configuration for a different product collation was a simple case of changing the recipe at the intuitive operator interface. This would change the amount of rotation for the final belt, allowing bundles of anything between two and ten products to be pushed to the sealer.
Glyn Johnson, YPS’ MD, said: We look to work with our customers to understand their exact needs each time, so we can deliver a system that works precisely as they want it to. Our engineering team bring their experience and knowledge to any situation, however unusual, so we can find the right solution.
The YPS engineering team implemented an innovative system on the sealing jaw to guarantee that the lightweight, vulnerable packs would pass through the sealing process without it activating, eliminating the possibility of damage to the packs.
The automatic l-sealer controls were paired with the shrink tunnel controls so that all parameters could be accessed from the same user interface, making the equipment easy to use and ensuring full control over the wrapping operation.
The specially configured shrink-wrapping line produced a neatly sealed product bundle each time and could be easily changed when different product collations were required.
Related News
-
Supplier News
YPS: ROI of less than 12 months for automated ecommerce bagging equipment
-
Supplier News
98% recycled-content flexible film now available from YPS
-
Supplier News
YPS: Pack consistency improved whilst increasing production speed for pharmaceutical manufacturer
-
Supplier News
YPS announce commitment to net zero by 2035
-
Supplier News
YPS: End-to-end automated packaging system streamlines ecommerce operation