Royal Apollo Group: How to choose the right vertical conveying system
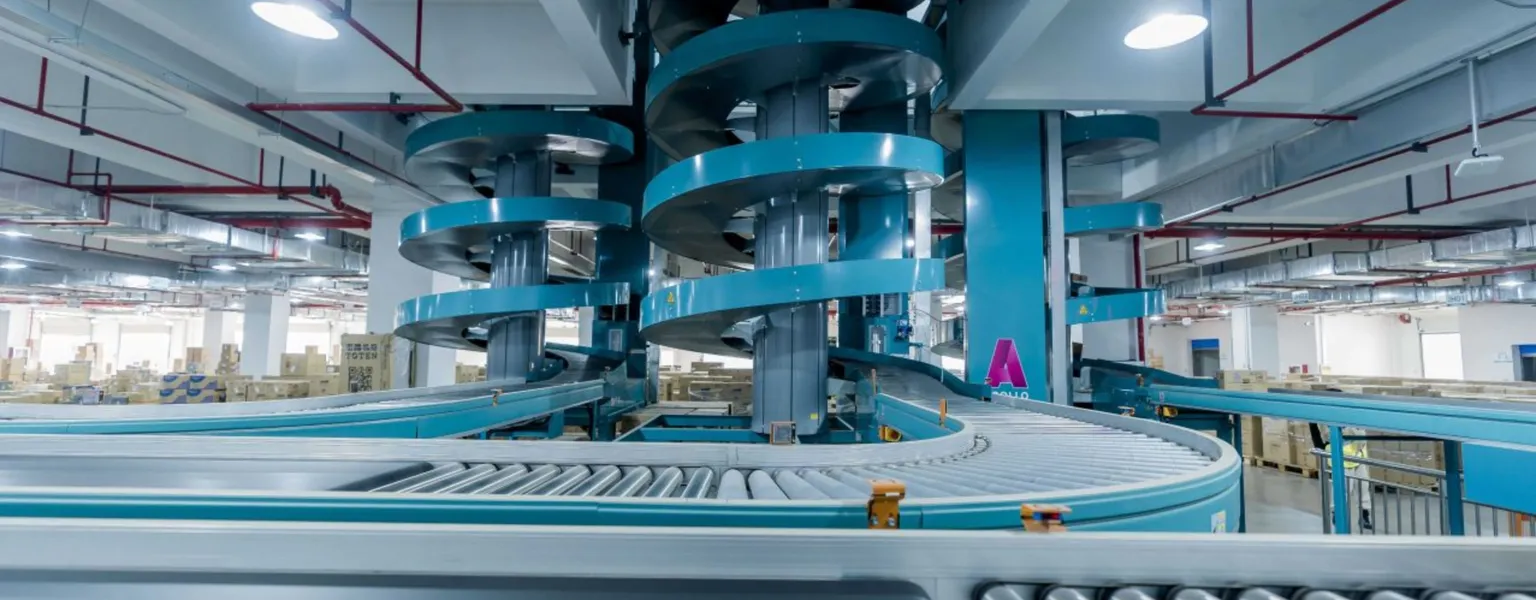
Supplier News
Vertical conveying systems are integral to various industries, ranging from manufacturing to warehousing and distribution. They are designed to move goods vertically, saving space and enhancing operational efficiency. However, choosing the right vertical conveying system for your specific needs can be a complex process. This blog will guide you through the essential factors to consider to make an informed decision.
1. Understand your needs
A. Type of material
Identify the types of materials you will be transporting. Are they bulk solids, liquids or packed items? Different systems handle different materials:
Bucket Elevators are ideal for bulk materials like confections, powders, pet food, coffee, hardware, seeds/nuts, grains & recycles/wastes.
Spiral Conveyors work well with packed products such as bags, bundles, totes, containers, shrink wrapped products, crates, tires, carton wrapped products, trays and cartons. Also mass products like bottles, cans, jars, cups and pouches are suitable for transportation on Spiral Conveyors.
B. Load capacity
Determine the maximum load capacity required. This includes the weight of individual items and the total weight the system needs to handle per cycle. Ensure the system can handle peak loads to avoid downtime and inefficiency.
2. Consider operational factors
A. Throughput requirements
Assess the speed and frequency at which you need to move materials. High-throughput operations may require continuous systems like spiral conveyors, while lower throughput needs might be met with VRCs.
B. Maintenance and reliability
Consider the maintenance needs and reliability of the system. Look for systems with proven track records and consider the availability of spare parts and technical support.
3. Evaluate system types
A. Bucket elevators
The Bucket Elevators are very well suited for a broad range of bulk products in the food, agriculture and different types of industries. The machine has many benefits:
Combining both horizontal and vertical transport.
Overlapping buckets = no spillage
Several inlet and outlet stations possible
Long-life, low maintenance
B. Spiral conveyors
Spiral Conveyors transports products up or down in a continuous flow and has proven to be a very reliable concept in Vertical Conveying. Royal Apollo Spiral Conveyors are designed according our proven reliable technology, offering many features and benefits:
Saving floor space
Increasing productivity
Reducing down-time
Low maintenance
4. Cost analysis
A. Initial investment
Calculate the upfront cost, including installation. More advanced systems may have higher initial costs but offer better long-term savings.
B. Operating costs
Factor in energy consumption, maintenance and potential downtime. Systems that require less frequent maintenance and use less energy can save money over time.
C. Return on investment (ROI)
Evaluate the expected ROI by comparing the cost savings from improved efficiency, reduced labor, and lower operational costs against the initial and ongoing expenses.
Conclusion
Choosing the right vertical conveying system is critical to optimizing your operations and achieving long-term efficiency and cost savings. By understanding your material handling needs, considering operational factors, evaluating different system types and analyzing costs you can make an informed decision that aligns with your business goals. Investing time and effort in this selection process will pay off in improved productivity and streamlined operations
This article was originally published by Royal Apollo Group.
Related News
-
Supplier News
Apollo VTS Asia showcases at ProPak Asia 2025
-
Supplier News
Discover the power of Apollo’s multiple infeed & outfeed spiral conveyor
-
Supplier News
Royal Apollo Group: 5 signs you need a conveyor upgrade
-
Supplier News
Royal Apollo Group: Logistics systems to optimise material flow and operations
-
Supplier News
Discover Apollo’s unique slat designs for material handling