PHS: Working smarter for commercial and industrial manufacturing efficiency
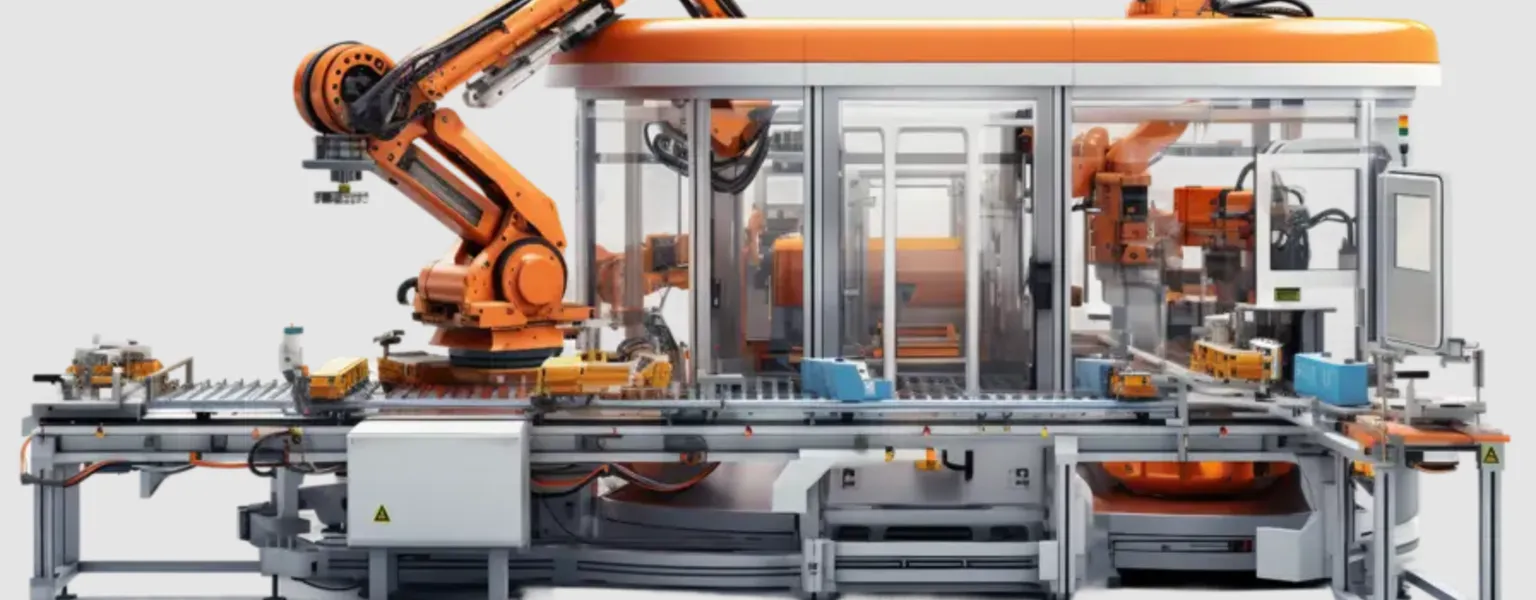
Supplier News
Businesses of all sizes face the logistics headache of unloading products and goods, both in industrial and commercial settings.
Here, we look at how a de-palletiser can help with efficiency and productivity for your business to help with the overall streamlining of operations.
Modern de-palletisers can handle a variety of product sizes, shapes, and pallet configurations, making them suitable for many diverse applications. They can be scaled up or down to meet changing production demands without the need for significant additional investment in what is a challenging time economically for businesses and operations of all sizes.
De-palletisers are machines designed to automatically unload products from pallets. They can handle high volumes of goods quickly, reducing the time required for manual unloading. By automating the unloading process, business owners can significantly reduce associated manual labour costs whilst safeguarding their workforce against injuries in the workplace.
Automated systems are more precise and gentle than traditional manual handling, which also helps with reducing product damage and unnecessary waste of damaged goods not fit for purpose. Systems can be scaled up or down to meet changing production needs without the need for any significant extra investment.
By ensuring the precise handling and placement of products, the associated processes down the line, such as sorting, packing and shipping, are also simplified. Integration with warehouse management systems allows for better tracking and traceability of inventory. They can be seamlessly integrated with other automated systems such as conveyors, robotic arms, and sorting machines, enhancing overall workflow efficiency.

With their compact design, many de-palletisers are designed to take up minimal floor space, helping to optimise the layout of warehouses and production facilities. An average de-palletiser may take up anywhere from 600 to 650 square feet of floor space, so the footprint of the machine is a key consideration when deciding which one to buy.
Add to this that they can provide valuable data on operational performance, which can be used for continuous improvement and optimisation.
Typically built to withstand heavy-duty use, de-palletisers are generally straightforward to maintain, ensuring long-term reliability and minimised downtime.
As with any large investment decisions, businesses need to consider their specific production requirements and the best solution to accommodate these.
A de-palletiser will not be the only machine required and depending on the materials being packaged, it may be cited alongside fillers, seamers, labellers and case packers, for example. Making efficient use of floor space is crucial. The de-palletiser may need to integrate with the other machinery and this is a vital component to consider as part of the buying process.
This article was originally published by Phoenix Handling Solutions.
Related News
-
Supplier News
PHS: Layer palletisers for beverages
-
Supplier News
PHS: Why efficient packing is not just for holidays…
-
Supplier News
PHS: Strapping in for success…
-
Supplier News
PHS: Packaged to perfection for industrial and commercial needs
-
Supplier News
PHS: How semi-automatic pallet wrappers are transforming the food industry