PHS: Five strategies to optimise stretch film usage in pallet wrapping
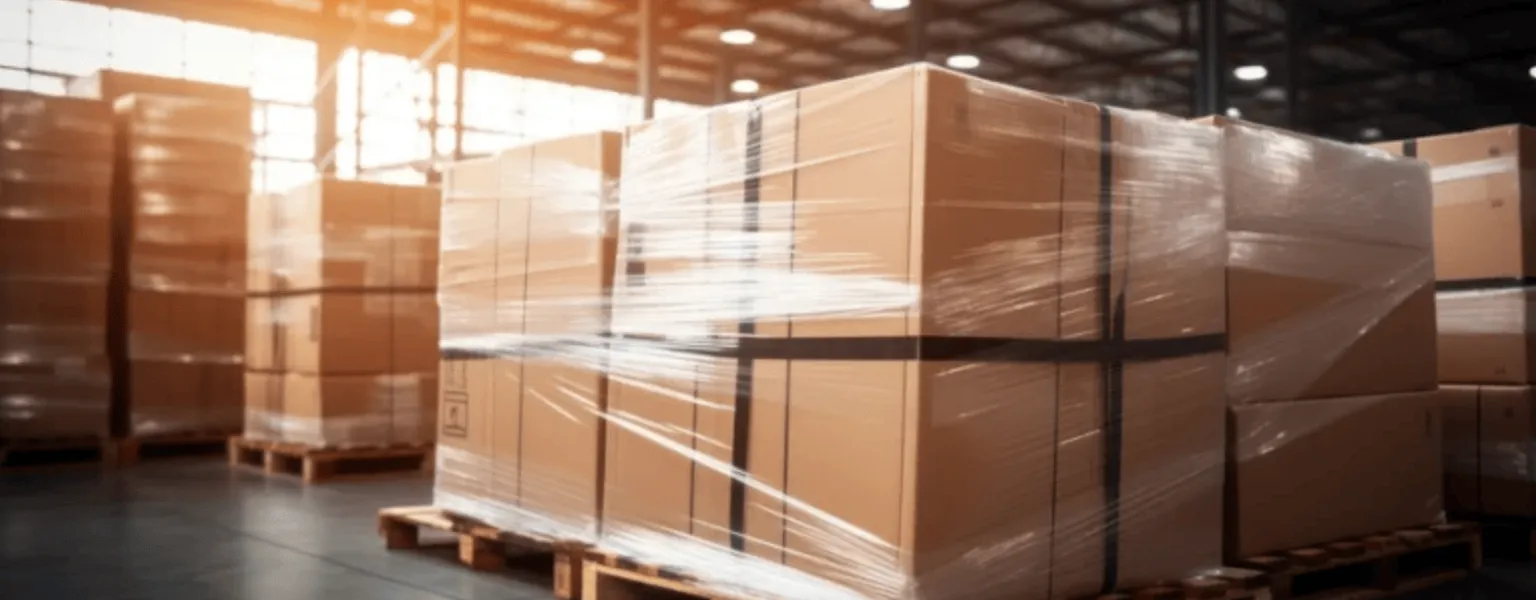
Supplier News
In a business environment where financial prudence is vital and environmental stewardship is a priority, the efficiency of stretch film usage in pallet wrapping is a critical concern. Businesses employing packaging systems are focusing on optimising stretch film use to fulfil their eco-friendly commitments and logistical objectives.
1. Selecting the right stretch film
The cornerstone of cost-saving in pallet wrapping is the selection of stretch film. While budget-friendly pre-stretched films are available, their effectiveness in securing loads can be subpar, necessitating more film to ensure safety and protection. It’s wise to invest in technical stretch films with lower thickness yet higher efficiency, which ultimately leads to less plastic use. These films feature enhanced pre-stretch capabilities and reduced gauge, contributing to both cost reduction and sustainability.
Understanding pre-stretch film efficiency
Pre-stretching stretch film involves extending the film before application to enhance its strength and coverage ability. Advanced stretch wrappers equipped with motorised or electronic pre-stretch systems can maximise this capability, typically offering 100% to 300% pre-stretch. Utilising the optimal pre-stretch level ensures a secure wrap while optimising film use.
The impact of 300% pre-stretch
Consider a standard pallet side measuring 1000 mm. With 300% pre-stretch, a film segment extends to cover three sides of the pallet, tripling efficiency. Over time, the cost benefits of a higher-performing pre-stretch film can outweigh the initial investment in a sophisticated stretch wrapper.
2. Thinner films for bigger savings
The use of thinner micron thickness films has become more prevalent in the pursuit of lighter packaging. These films have been reduced from the typical 20-30 microns to as little as 10 microns. These advanced films are created using high-stretch, puncture-resistant linear low-density polyethylene (LLDPE), which maintains or even enhances wrapping integrity while using less material.
3. Stretch wrapper features that enhance savings
A stretch wrapper’s features can greatly influence film consumption. Here are a couple of significant aspects to look for:
- Advanced pre-stretch systems: A sophisticated mechanism equipped with mechanised or electronic controls is utilised to ensure precise and efficient film consumption, in addition to the use of high pre-stretch films that can stretch up to 400%.
- Torque control system: This feature finely tunes the force exerted during wrapping, allowing for meticulous control over film tension and elimination of waste.
4. Refining the wrapping cycle
To make real savings, the entire wrapping cycle must be scrutinised and programmed for efficiency, focusing on:
- Strategic reinforcement: Applying more film at critical points for stability, especially at the pallet base.
- Targeted containment force: Adjusting the film tension to the requirements of different pallet areas.
- Roping techniques: Where applicable, using roping devices to enhance stability with fewer film rotations.
- Minimised waste: Ensuring no excess film tails remain, aligning film application strictly with load securing needs.
5. Integrating into logistic operations
Finally, a stretch wrapper’s role at the logistics end cannot be understated. Automated packaging systems mitigate human error, enhance load security, and prevent transportation losses. A well-integrated stretch wrapping system contributes to a seamless logistics chain, adding value by preventing material damage and loss.
The successful integration of film selection, wrapper features, and optimised operational protocols is essential for achieving significant cost reductions and promoting sustainability in the packaging process. By strategically implementing these five key elements, a stretch wrapping operation can become more efficient, environmentally conscious, and economically viable.
This article was originally published by Phoenix Handling Solutions.
Related News
-
Supplier News
PHS: Layer palletisers for beverages
-
Supplier News
PHS: Why efficient packing is not just for holidays…
-
Supplier News
PHS: Strapping in for success…
-
Supplier News
PHS: Working smarter for commercial and industrial manufacturing efficiency
-
Supplier News
PHS: Packaged to perfection for industrial and commercial needs