Delkor: Maximizing efficiency – how case packers can help combat rising costs
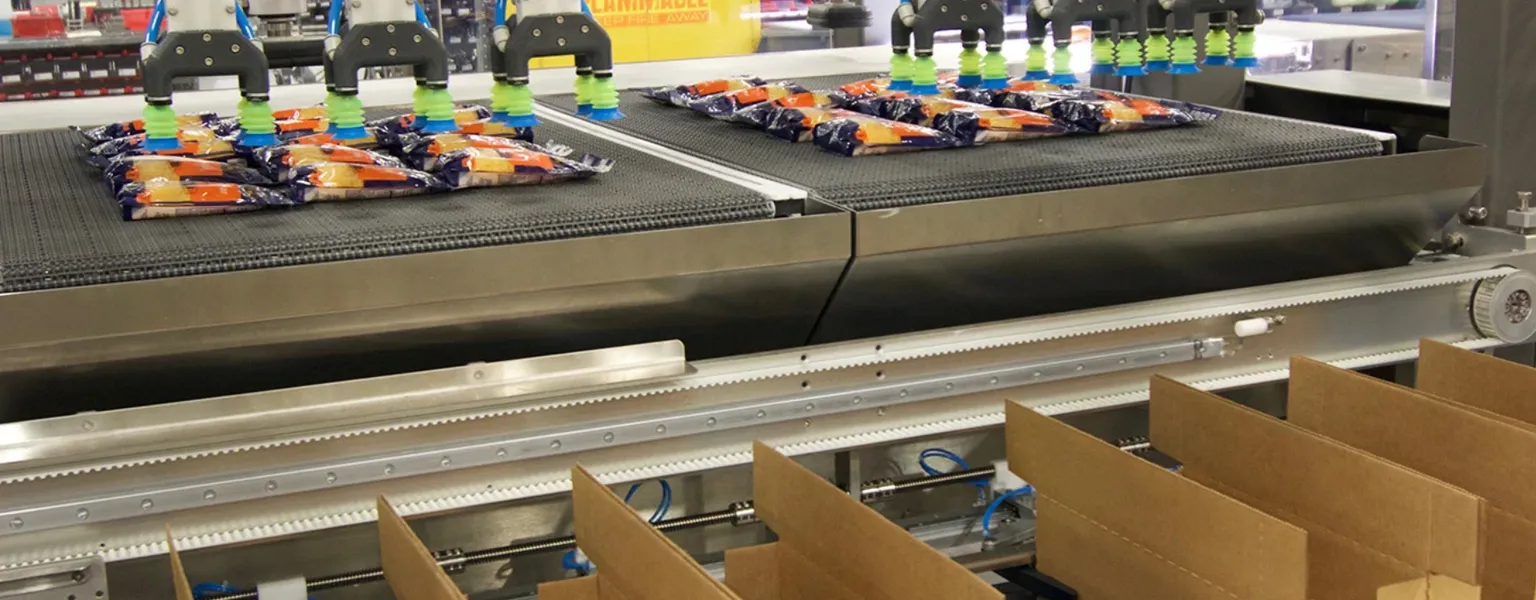
Supplier News
If you’ve been to the grocery store or a restaurant lately, you’ve undoubtedly noticed that food costs are at an all-time high. In fact, according to Yahoo Finance, food costs have risen approximately 25.8% since 2020 alone. There are many factors that play into this, of course, but at the end of the day, costs have increased and consumers across the globe are feeling it. If you’re a manufacturer in the food industry (or any industry really), how can you combat rising costs?
One of the most obvious solutions is to maximize production efficiencies. There are a number of ways to do this but as manufacturers of packaging equipment, we’re going to cover how improving your packaging operations can lead to cost savings and an improved bottom line.
The first step in maximizing packaging production? Securing the right equipment. For many companies, that starts with finding the right case packer for your products. Case packers, or specialized machines designed to automate the product packing process, take products of nearly any size and shape and place them into cases, cartons, club store trays, etc. for secure distribution. Every application is unique but for the most part, the process looks something like this:
First, the packing process begins with feeding the product into the case packer. Depending on the specific design of the machine and the type of product being packed, this step can involve conveyor belts, robotic arms, or other feeding mechanisms. Manual feeding is another option, of course, but not if maximizing efficiency is the end result.
Once products are fed into the machine, they’re grouped and oriented according to the desired packing configuration. This ensures products are arranged efficiently within the case, maximizing space utilization and minimizing waste. With Delkor case packers, companies can configure their packing in nearly any pattern, making it easier than ever to safely and securely pack products in a way that makes the most sense for the application.
Then, when cases, cartons, club trays, etc. are at full capacity, the case packer moves them to the closing and sealing step. In order to fully automate, this step would include another machine, a closer, which seals and closes cases. Obviously, continuing to automate the process will positively benefit efficiency rather than doing so manually.
With the basic operation of case packers defined, let's explore why using case packers in your production process could help combat rising operations costs.
1. Efficiency
Case packers automate what would otherwise be a labor-intensive and time-consuming process. By streamlining packing operations, these machines significantly increase throughput and reduce labor costs, allowing companies to meet growing demand with ease. Though the initial cost may be high, we see many customers “pay” for the investment with the material savings and labor costs recognized as early as 18 months after installation.
2. Accuracy
Manual packing processes are prone to errors and inconsistencies. After all, humans can’t be perfect 24/7. On the contrary, case packers CAN ensure products are packed uniformly and securely every time, minimizing the risk of damaged goods and customer dissatisfaction.
3. Flexibility
As mentioned earlier, many modern case packers are highly versatile and can accommodate a wide range of product types, sizes, and packaging configurations. This flexibility makes them suitable for use across diverse industries, from food and beverage to pharmaceuticals and consumer goods. Additionally, this flexibility (at least with Delkor case packers), allows manufacturers to run multiple shipper styles on one machine with minimal changeover downtime.
4. Safety
One could argue that safety violations or accidents don’t directly contribute to rising costs but minimizing safety is always a good goal to have in place. And, by automating repetitive and potentially hazardous tasks, case packers can help contribute to a safer work environment for employees by reducing the risk of workplace injuries.
If you’re still not convinced that implementing a case packer or packers into your operations would benefit your bottom line, we encourage you to reach out to one of our packaging specialists. We may be biased but we truly believe case packers play a pivotal role in modern packaging operations, providing the speed, accuracy, and efficiency needed to meet the demands of today's market and battle ever-increasing costs.
This article was originally published by Delkor.
Related News
-
Supplier News
Delkor automation brings big benefits to employees and bottom line
-
Supplier News
Delkor introduces Rapid Delivery Program for carton formers & closers
-
Supplier News
Delkor unveils revolutionary case packer technology at PACK EXPO 2024
-
Supplier News
Delkor's inventive mindset strengthens lead in retail-ready market
-
Supplier News
Delkor leads cheese packaging with unmatched, versatile solutions