Coca-Cola Bottlers Japan Unveils New Ebina Plant with AmbaFlex SpiralVeyor Solutions
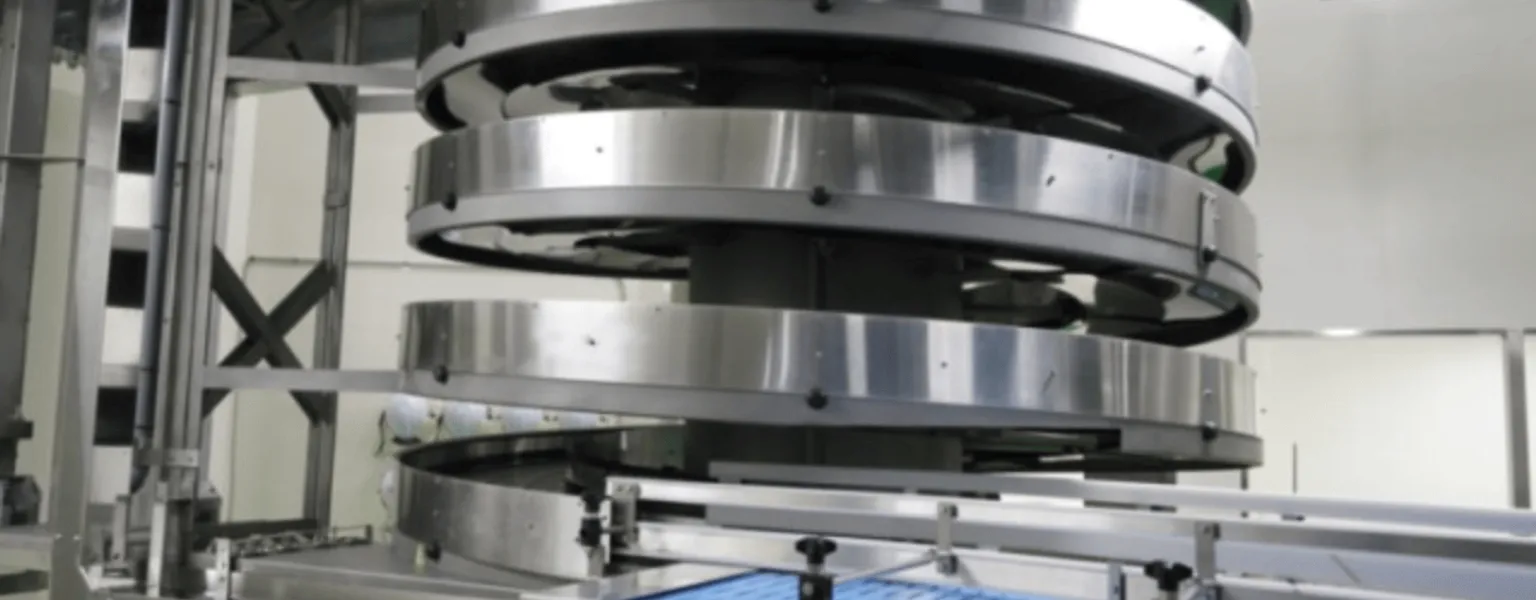
Supplier News
On May 29th, Coca-Cola Bottlers Japan proudly unveiled its state-of-the-art Ebina Plant located in Ebina City, Kanagawa Prefecture. The media event showcased the introduction of a cutting-edge aseptic production line, known as the new line No. 5.
AmbaFlex, a trusted partner in material handling solutions, played a crucial role in this milestone achievement. We successfully delivered two SpiralVeyor types SVm for Mass Flow handling and one SpiralVeyor SV for the Ebina Plant. These SpiralVeyors were specifically designed to optimize space utilization within the facility while efficiently handling a remarkable 900 bottles per minute. Their remarkable throughput speed ensures seamless operations for products ranging in size from 190 ml to 500 ml.
The introduction of the new line No. 5 marks a significant expansion in the production capacity for small PET bottle products, which are experiencing a surge in demand. This expansion necessitated an increase in aseptic filling capabilities and enhanced transportation efficiency throughout the company. As a result, the supply of canned coffee products, which were previously manufactured on the old No. 5 line, will now be covered by production at other plants.

AmbaFlex's reliable and space-saving SpiralVeyor solutions have proven instrumental in supporting Coca-Cola Bottlers Japan's drive for increased productivity and flexibility. Our partnership continues to deliver innovative solutions that meet the evolving needs of the beverage industry.
Atsuyuki Hatogai, Plant Manager of the Tama/Ebina Plant, SCM Division, who also serves as Plant Manager of both the Ebina and Tama plants, commented on the features of the new line: The latest technology in the beverage industry is that the evolution of aseptics has made it possible to sterilize milk powder by adding it to the line at the same time. The production capacity of this line is 900 bottles per minute, but since it is technically difficult to find a machine such as a labeler, which requires precision, that can exceed 900 bpm, two 450 bpm labelers are used for labeling in two separate steps. All beverage manufacturers have been restrained from developing new products due to the Corona disaster, but development will accelerate in the future. We would like to firmly establish our production and production line systems to respond to this trend, so that we can offer new products.
Related News
-
Supplier News
Charge your battery production efficiency with AmbaFlex spiral conveyors
-
Supplier News
AmbaFlex: Boosting bakery efficiency with smart accumulation solutions
-
Supplier News
AmbaFlex enhancing Airport Baggage systems
-
Supplier News
AmbaFlex to exhibit at FRUIT LOGISTICA 2025
-
Supplier News
Ambaflex: Cut costs by choosing for synergy