AmbaFlex: Grand opening of Canton production plant expansion
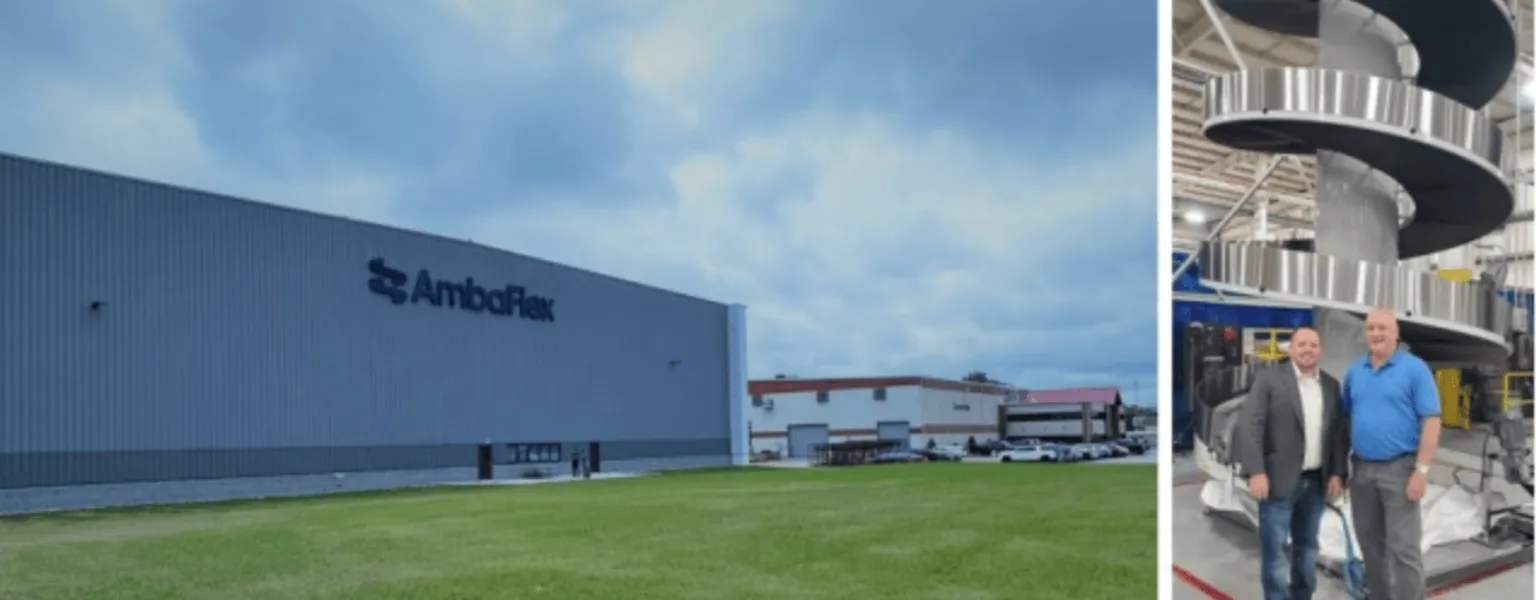
Supplier News
This article was originally published by AmbaFlex. The content originated by interviewing Mr. Phil Miller, President of AmbaFlex, Inc. and Mr. David Spencer, Vice President & Operations Plant Manager, AmbaFlex Manufacturing, Inc.
With 53,000 square feet of additional office and production space, AmbaFlex has reached a new milestone in their development with the grand opening of our plant expansion in Canton, Ohio. This makes us the largest spiral conveyor manufacturing facility in North America; a fact we’re proud of as the world leader in spiral conveying technology. We anticipate that by increasing the available footprint for operations, we immediately added 40% in production floorspace. With this expansion, we have created the capability to build up to 50 fully functioning machines per week!
Phil Miller: The new facility allows space for improved capacity and efficiency in our processes and operations, allows us to ensure lead times, innovate and upgrade our offerings, improve customer return on investment, provide faster and wider solutions for ever-changing market needs, and increase flexibility to accommodate new customer applications. We will now be able to provide a higher level of customer satisfaction regarding product quality, overall responsiveness, customer training opportunities, and overall customer service. A safer working environment for our AmbaFlex team brings world-class products and solutions to our customers.
Over the last 26 years, AmbaFlex has experienced consistent, year-on-year growth. We may have started close to Amsterdam in 1997, but a mere thirteen years later, the demand for SpiralVeyors in North America equaled the demand we were experiencing in Europe. It was then decided that a US manufacturing facility was needed. Our first “Made in the USA” spirals were produced in an 8,000 square foot building that was opened in October 2010 less than a mile from our current manufacturing campus.
As you can imagine, the first two years of operations were pivotal as customer demand proved that there was much potential within North and South America for AmbaFlex. Because of that early growth and our commitment to customer satisfaction, investing in a much larger manufacturing facility was an easy decision in early 2013. From 2013 to 2019, support departments were introduced step by step in Canton’s 98,000-square-foot factory: Customer Service, Human Resources, Order Management, Purchasing, Finance, and Spare Parts. Each addition provided crucial benefits for our customers in North and South America, making it easier to do business together. Aided by these investments in equipment and staffing, the company experienced steady growth through 2019. The period from 2019 to 2022 represented the most significant increase in demand that AmbaFlex Inc. had ever experienced, fueled by the impact of the COVID pandemic.
David Spencer: The new facility was instrumental in our continued development and allowed us the space needed for our internal fabrication activities. We have added a laser cutter, two CNC press brakes, blast cabinet, and milling equipment to effectively allow AmbaFlex to fabricate short-run parts internally. This investment allows the company to keep its lead times competitive, even on specialty orders. Further, we added injection molding activities to the facility to meet the needs of our customer base in the AMCAS region. The facility in Canton will be able to produce over 98% of the required slats for the region.
The expansion has also impacted the spare part capabilities for the AMCAS region. We have introduced automation into our warehousing activities through the Modula VLM Lift. This automation will streamline our internal processes and reduce the time from spare part orders being received to shipment. This same technology will be helpful with service requests for parts.
By installing the new warehouse racking system and Turret lift technologies to maximize warehouse space, AmbaFlex ensures that it maintains a lean but flexible operation.
Another investment we have scheduled for the end of this year is the completed setup of a ‘Testing & Demonstration Area’ within the Canton facility. Here, we can demonstrate and test customer products on our different technologies: multiple SpiralVeyor configurations, AccuVeyor solutions, and the AmbaVeyor products. With more than 300 available variations, we can meet the material handling demands of our customers in E-Commerce/Warehousing, Packaging and Bottling & Canning.
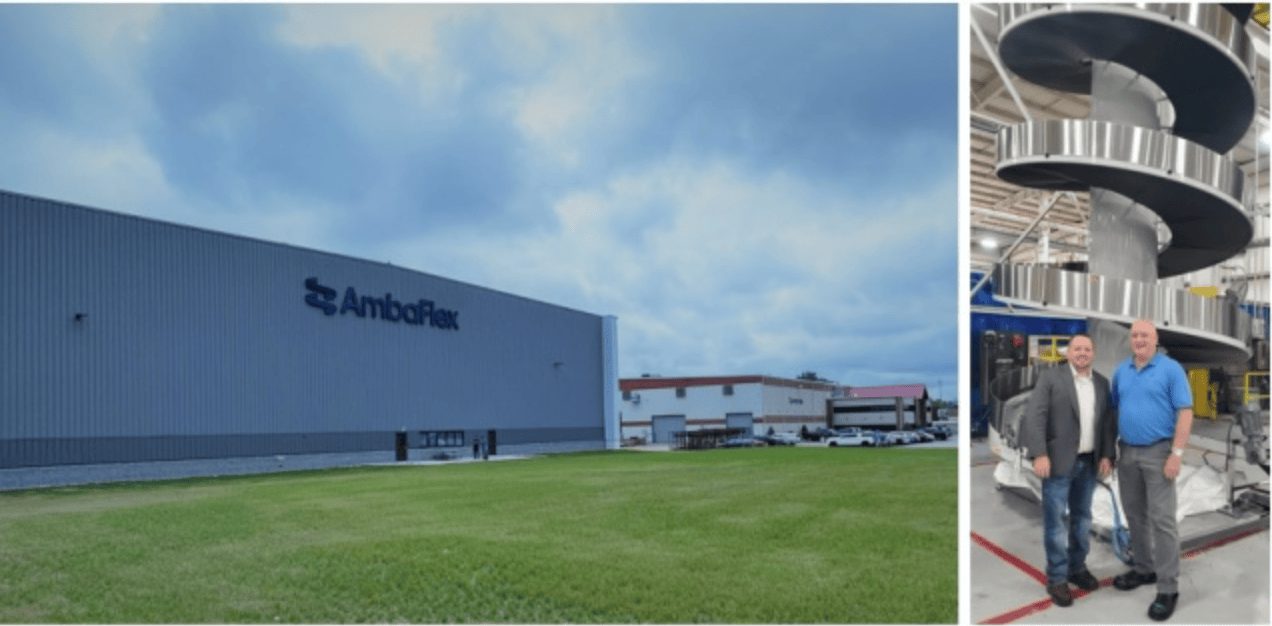
AmbaFlex is dedicated to fulfilling the demands of our customers. The organization and facility investments made since 2010 demonstrate this. Customer satisfaction is the achieved result of increased production capacity, improved lead times, cost and quality management, and improved response times to meet customer needs. We invite you to visit, discuss what we can do for you, and witness how the machines are built from raw steel to fully functioning, space-saving equipment that fits perfectly in your warehousing or production environment. We look forward to meeting you in Canton, Ohio, soon!
Related News
-
Supplier News
Charge your battery production efficiency with AmbaFlex spiral conveyors
-
Supplier News
AmbaFlex: Boosting bakery efficiency with smart accumulation solutions
-
Supplier News
AmbaFlex enhancing Airport Baggage systems
-
Supplier News
AmbaFlex to exhibit at FRUIT LOGISTICA 2025
-
Supplier News
Ambaflex: Cut costs by choosing for synergy