IVS: 3 simple steps to improve your machine vision system
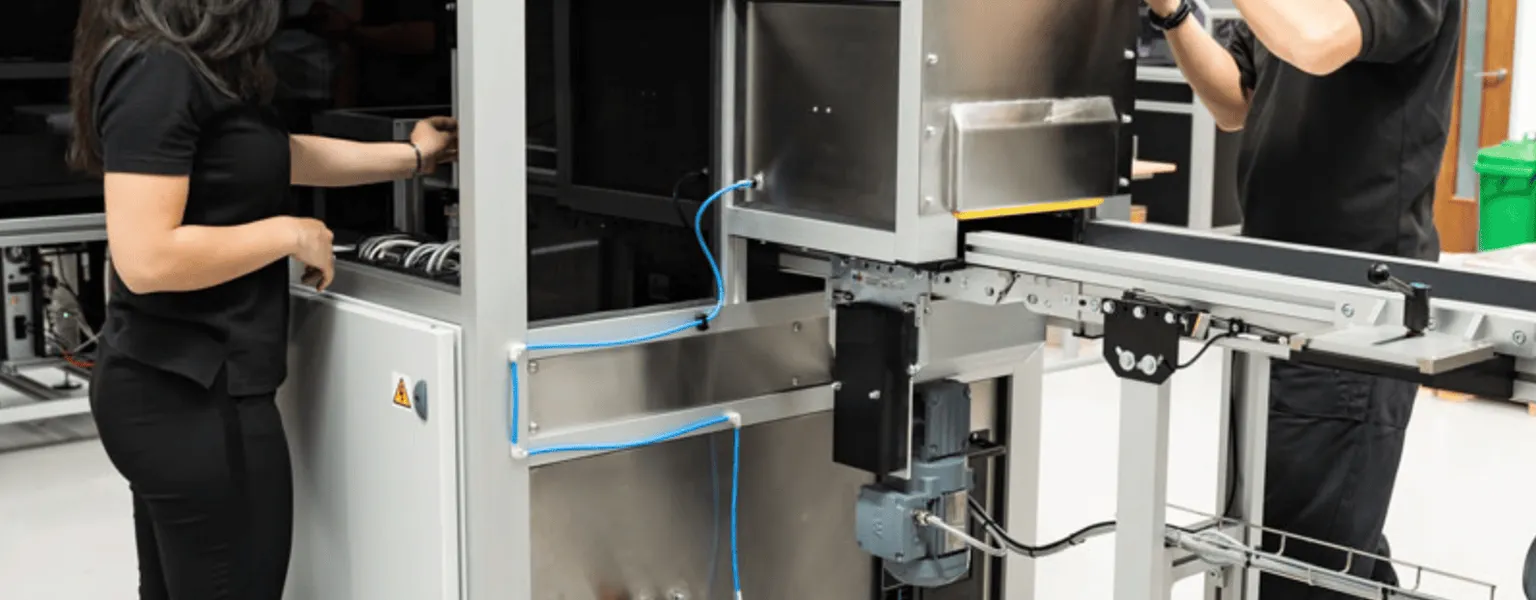
Supplier News
What's the secret to a perfect vision system installation? That's what all industrial automation and process control engineers want to know.
The engineering and quality managers have identified a critical process requiring automated inspection, so how do you guarantee that the machine vision system has been set up to the best possible engineering standard. And how can you apply this knowledge to refine the current vision systems on the line? Let's look at some of the critical parts of the vision inspection chain and see the vital elements and what needs to be addressed. IVS has been commissioning machine vision systems for over two decades, so we understand the core elements inside and out of vision system installs. Use some of our tricks of the trade to improve your vision system. These 3 simple steps to improve your machine vision system will help you understand the immediate changes you can make to improve a vision system.

Step 1 - lighting and filters
What wavelength of light are you using, and how does this compare to the sensitivity of the camera, coupled with the colours on the part requiring inspection? An intelligent approach to how segmentation of the scene will take place should be based on the correct lighting set-up, the angle of the machine vision lighting and how the contrast is created based on the colour of the part against the light, either reflecting to or away from the camera. Coloured illumination may intensify or suppress defined colours in monochrome imaging. This way, the contrast helps recognise relevant features, which is decisive for an application-specific and optimally matched vision solution. For example, blue light cast onto a multi-colour surface will only be reflected by the blue content. The more blue content in the object, the more light is reflected, so the brighter the object will appear. In contrast, red content illuminated in blue appears exceptionally dark.
Combining, a filter mounted on the end of the lens allows blocking all unwanted ambient light and passing only the necessary wavelength of light required, increasing contrast and resolution. The choice of which filter to use depends on the type of result you are trying to achieve. But selecting an appropriate filter may improve your current system's quality if ambient light is a problem for you.
Bandpass filters are frequently one of the simplest methods to significantly improve image quality. They have a Gaussian transmission curve and are ideal for investigating the effects of monochromatic imaging. But what are the different filters available?
Multi Bandpass Filters
Multi-Bandpass Filters use a single filter to transmit two or more distinct wavelength bands. They provide natural colour reproduction during the day and near-infrared illumination at night, resulting in accurate, high-contrast pictures. As a result, these are more suited for applications including intelligent traffic solutions, security monitoring, and agricultural inspection.
Longpass Filters
Longpass Filters enable a smooth transition from reflection to transmission and are available in various wavelengths based on the system's requirements. Longpass filters are an efficient method for blocking excitation light in fluorescent applications and are best employed in a controlled environment where several wavelengths must be passed.
Shortpass/NIR Cut Filters
Shortpass filters offer an unrivalled shift from transmission to reflection and superb contrast. They work best in colour imaging to ensure natural colour reproduction and prevent infrared saturation.
Polarising Filters
Polarising filters minimise reflection, increase contrast, and discover flaws in transparent materials. They're ideally suited for tasks requiring a lot of reflection, such as analysing items on glossy or very shiny surfaces.
Neutral Density Filters
Neutral Density Filters are known in the machine vision industry as "sunglasses for your system" because they diminish light saturation. Absorptive and reflective styles are available and are ideally suited for situations with excessive light. They offer excellent methods for controlling lens aperture and improving field depth.
So how do you match the filter to the light? Well, the LED's nanometers (nm) wavelength typically relates to the band pass rating for the filter. So if you work in UV at 365 or 395nm, you would use an equivalent rated filter – BP365. If you're using a green LED at 520nm, this would be a 520 band pass filter, and so forth. According to the filter rating, most filters have a curve chart to see where the light is cut-off.
Step 2 - camera resolution and fields of view (fov)
A vision system's spatial resolution refers to the sensor's active available pixels. When reviewing an improvement in your set-up and understanding where the fault may lie, it's important to consider how many pixels you have available for image processing relative to the size of the defect or computation you are trying to achieve. For example, if you are trying to defect a 100 micron (0.1mm) x 100 microns (0.1mm) inclusion on the surface of a product, but the surface is 4m x 4m in size, by using a standard 5MP camera (say 2456 x 2054 pixels) you will only be able to resolve a single pixel to at best 4000/2054 ~ so 1.9mm. This is nowhere near the level of detail you need for your imaging system. So to improve your machine vision system, see what size of a defect you need to see and then work out your field of view (fov) relative to the pixels available. But bear in mind having a single-pixel resolution for your measurement is not good enough, as the system will fail the Measurement Systems Analysis (MSA) and Gauge R&R studies (These are tests used to determine the accuracy of measurements).
In this case, you need to be at a minimum of 20 pixels across the measurement tolerance – so 0.2/20 = 0.01mm. Therefore, you will need 10 microns per pixel for accurate, repeatable measurement – over 4m; this is 400,000 pixels. So the 5MP pixel camera original specified will never inspect one shot – the camera or the object will have to be moved in small fields of view or larger resolution cameras specified for the system to hit the inspection criteria.
Step 3 - vision algorithm optimisation
One of the major steps for improving a machine vision system is a thorough review of the vision system software and the underlying sequence of inspection for the image processing system. If the system is a simple, intelligent vision sensor, it might be a matter of reviewing the way the logical flow of the system has been set. Still, for more complex PC-based vision applications, there will be some fundamental areas which can be reviewed and checked.
1. Thresholding
Thresholding is a simple look-up table that places pixel levels into a binary 1 and 0 depending on where they sit above, below or in-between two levels. The resulting image is a pure black and white image, then used to segment an area from the background from another object. Dynamic thresholding is also available, which intuitively sets the threshold level based on the pixel value distribution. But because it uses the fundamental pixel grey level to determine the segmentation, it can be easily affected by changes in light, as this will ultimately change the pixel value and lead to changes required to the threshold level. This is one of the most common faults in a system which has not been set up with a controlled lighting level. So if you are reviewing a threshold level change, you should also check the lighting and filters used on the system, as seen in Step 1.
2. Calibration
Perhaps not calibration in the true sense of the word, but if the camera on your vision system has been knocked out of place (even slightly), it may have detrimental effects on the inspection outcome and the yields of the vision system. Re-calibration may need to be done. This could initially be checked, as most modern systems have a cross-hair type target built into the software to allow a comparison image from the original system install to be compared with a live image. Check the camera is in-line, and the field of view is still the same. Focus and light should also be consistent. Some measurement-based machine vision systems will come shipped with a calibration piece or a Dot and Square Calibration Target. These generally come with a NIST Traceability Certificate, so you know that the artefact is traceable to national standards. This calibration target should be placed, and the system checked against it.
So these 3 simple steps to improve your machine vision system may just help you increase your vision system's yield and stop the engineering manager from breathing down your neck. This will ultimately enhance your production productivity and advance the systems in use. And remember, you should always look at ways to reduce false failures in a vision system; this is another way to boost your vision system performance and improve yield.
This article was originally published by Industrial Vision Systems Ltd. (IVS).