ISRA VISION's PrintSTAR enhances quality in packaging film printing
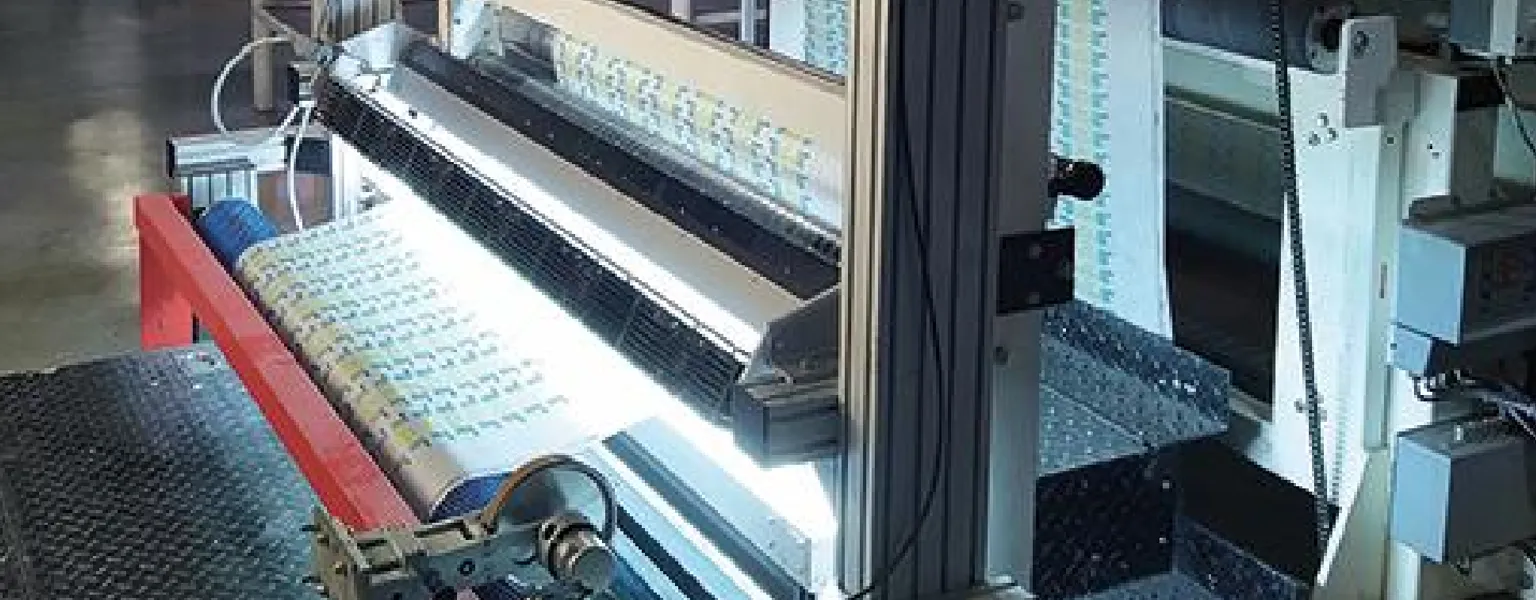
Supplier News
100 % inline inspection in one of France's largest print shops
G'imprim, a division of the GRANGER Group, runs one of the largest print shops for flexible packaging in France. They chose PrintSTAR, the 100% inspection system from ISRA VISION, to mitigate quality issues in their printing and prevent customer complaints.
With seven 8-to-10-colour flexo lines offering a scalable capacity of up to 600 million linear meters per year, G'imprim prints flexible packaging for large customers. Its product range extends from shrink films for the beverage and canning industry, packaging films for pulp producers (kitchen/toilet paper rolls), and films for FFS sacks made from PPE to breathable and standard films for hygiene products.
High-quality packaging provides both a key marketing message and a purchase incentive at the point of sale, often making it crucial to purchasing decisions, especially for first-time customers. The quality - suggested by its appearance and the expectations it raises at the consumer - has a direct impact on how well a product sells. Defects in the printed image on the packaging, such as ink splashes or gaps, are not acceptable and should never make it as far as the retailer. They suggest that the product is of poor quality, damaging the brand perception and ultimately affecting sales. That is why standards for packaging print quality are so high today.

Improved product quality
As the previous inspection solutions no longer met the print shop's quality requirements, G'imprim has chosen a new system. The company was already very satisfied with ISRA VISION SMASH for unprinted plastic films and non-wovens.
Operating in another division, the 100% inspection systems been proven to be constantly reliable and very user-friendly since their successful trial phase in March 2014. The company was therefore keen to use another product from ISRA VISION.
To achieve sustainable and repeatable improvement in inspection performance and thus product quality, the PrintSTAR system for 100% web monitoring was chosen. PrintSTAR effectively complements the partial images made by matrix cameras from competing systems. Built around high-resolution line cameras, the system offers significant benefits in the inspection of continuous material, in particular, detecting even the tiniest defects missed by solutions that use matrix cameras. Combined with ultra-bright LED lighting, the 100% solution from ISRA VISION enables continuous quality and process monitoring of the printed image, lamination, and coating. PrintSTAR detects and classifies any emerging defects in real-time so that their causes can be rectified early.
Initial results in record time
The new inspection system was ready for operation and in productive use, one week after installation began. Since then, PrintSTAR has provided a guaranteed level of quality in numerous ways – which is especially clear in the reduced level of waste, the time and money saved by increasingly infrequent repeat production, and significantly fewer customer complaints.
High-performance defect detection and classification ensure that only relevant defects are reported. Furthermore, the system has particularly fine configuration capabilities. One of the first outcomes of the new system was the ability to identify recurring defects and implement tailored action plans to address them. 100% inspection allows the machine settings to be adapted in the best possible way, reducing the defect rate. The production analysis also proved to be useful when selecting the most suitable consumables for the printing presses themselves.
Installing the inspection system went perfectly, with no need for mechanical changes to the printing presses. Integrating additional modules into ISRA VISION's PrintSTAR 100% inspection system, such as ColorSTAR for monitoring colour accuracy or ViewSTAR for detecting the tiniest details during web monitoring, is the obvious choice for the future. The next step toward monitoring the process and the system status itself (condition/health monitoring) will soon be available through new software upgrades, such as EPromi Live. Options like this allow the system to be adapted individually to any customer's print task.
Economies of scale across the company
Staff quickly adopted the system as a useful and reliable tool that allows them to maintain a guaranteed quality level during production. Three departments in particular benefit directly from the use of the inspection system. For the printers, PrintSTAR both makes their day-to-day work easier by identifying defects and giving them the certainty of knowing that no relevant defects have been missed. With manual inspections now being outdated, they can take on other important tasks in other areas. Quality assurance staff uses the collected data to take optimisation measures across the entire printing process. In sales, significantly reduced defect numbers plus the option of creating qualified quality reports provides a strong value proposition for existing and new customers.
Better products and more satisfied customers
Although Print Star's 100% print quality inspection appears to have primarily internal effects, it also has a positive impact on the company's external image and customer perception. The automatic defect detection not only supports the print staff in their work. It also enhances machine productivity and ensures consistently high quality. As a result, G'imprim benefits from both improved product quality and decreased complaints. In addition, 100% inspection and the ability to provide corresponding quality reports is a strong appeal for old and new customers alike. This gives sales a powerful tool for enhancing customer relationships.
This article was originally published by ISRA VISION.