Improving the efficiency of farming operations with silage film Silotite1800
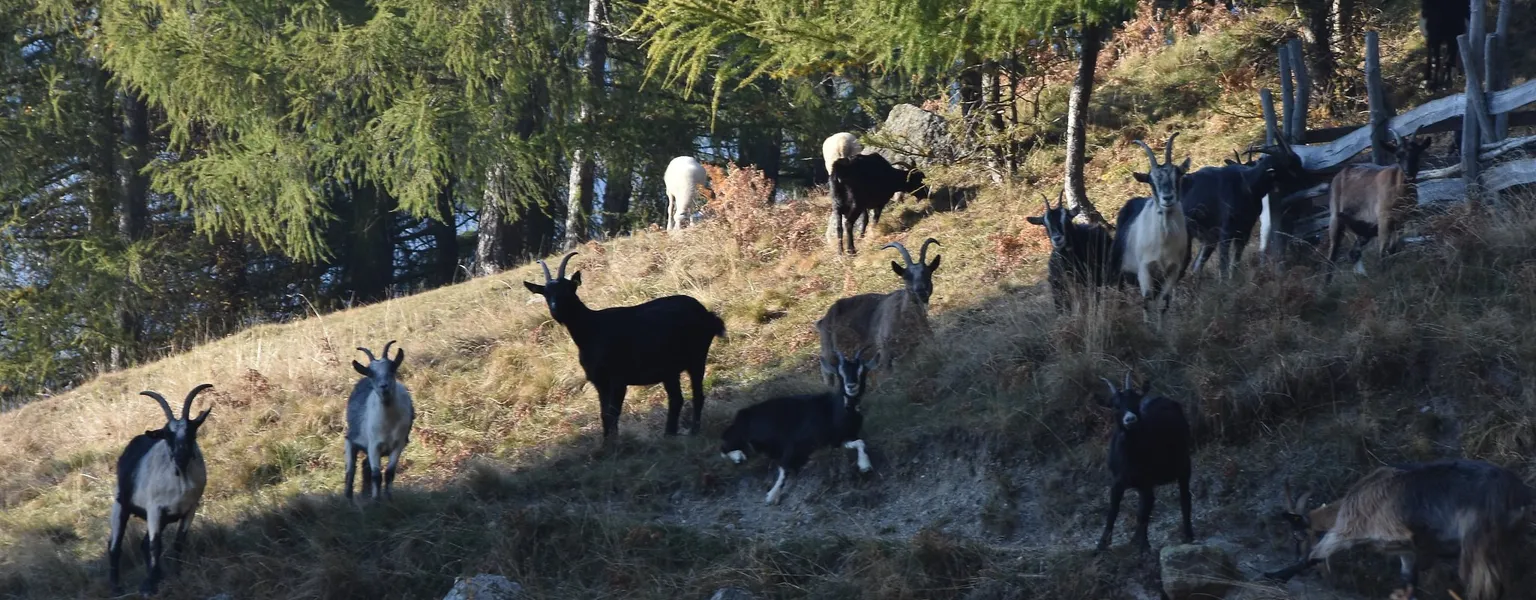
Supplier News
Gary and Jess Yeomans run a family owned 300-acre goat milking farm in Abergavenny, Wales. With more than 1,000 head of goats milked twice a day, the couple produces an average of more than 1,100 liters of milk per head that is converted into farmhouse cheese and sold locally.
Challenge
Goats are prone to developing listeriosis and acidosis in the absence of a properly protected food source, making a durable silage film crucial to their health and ability to produce milk that is sufficient for human consumption. While a regular silage film fulfilled this essential need for the Yeomans’ goats, the couple’s time was often occupied by routine checks for silage rips and tears and the handling, transportation, storage, and recycling of the film’s bulky box packaging. As an important source of dairy for their community, the Yeomans needed a more efficient way to meet the demands of local consumers.
Solution – Silotite1800 silage film
To ensure protection from forage contamination and streamline their farm operations, the Yeomans switched from a regular silage film to Silotite1800. Developed using the latest raw materials and advanced manufacturing techniques, Silotite1800 enhances the essential characteristics of silage stretch film, providing enhanced protection from bacteria and mould, whatever the weather. The films unique sleeve packaging design allows for more bales per reel compared to traditional films, eliminating downtime associated with managing bulky boxes.
Results
Since switching to Silotite1800 the Yeomans received first place at the FWGS Big Bale Silage competition for a combination of best practice methods and using the right products for the job. Their new silage film significantly improves the efficiency of their daily operations through its durable film properties, unique sleeve design, and enhanced reel capacity.
With a reliable oxygen barrier and UV protection, Silotite1800 shields the Yeomans’ forage from rain and contaminants, eliminating the need for frequent monitoring of silage rips and tears. Further, the sleeve package is made from the same film as the bale wrap, eliminating the need for bulky boxes. As a result, the Yeomans have seen a 20% reduction in handling, transportation, and storage space and no longer have to separate recycling materials.
This article was originally published by Berry Global.
Related News
-
Business
Durable bottle solution created for Vamoosh Plug Hole Unblocker
-
Supplier News
Not all tethered closures are equal: Consumer satisfaction is key to success
-
Business
Amcor and Berry Global shareholders overwhelmingly approve merger
-
Supplier News
Berry demonstrates how small is still exclusive
-
Supplier News
Berry Global and VOID Technologies collaborate to launch high-performance, sustainable film for pet food packaging