Adelphi Masterfil: AdBlue – Overcoming your most frequent filling challenges
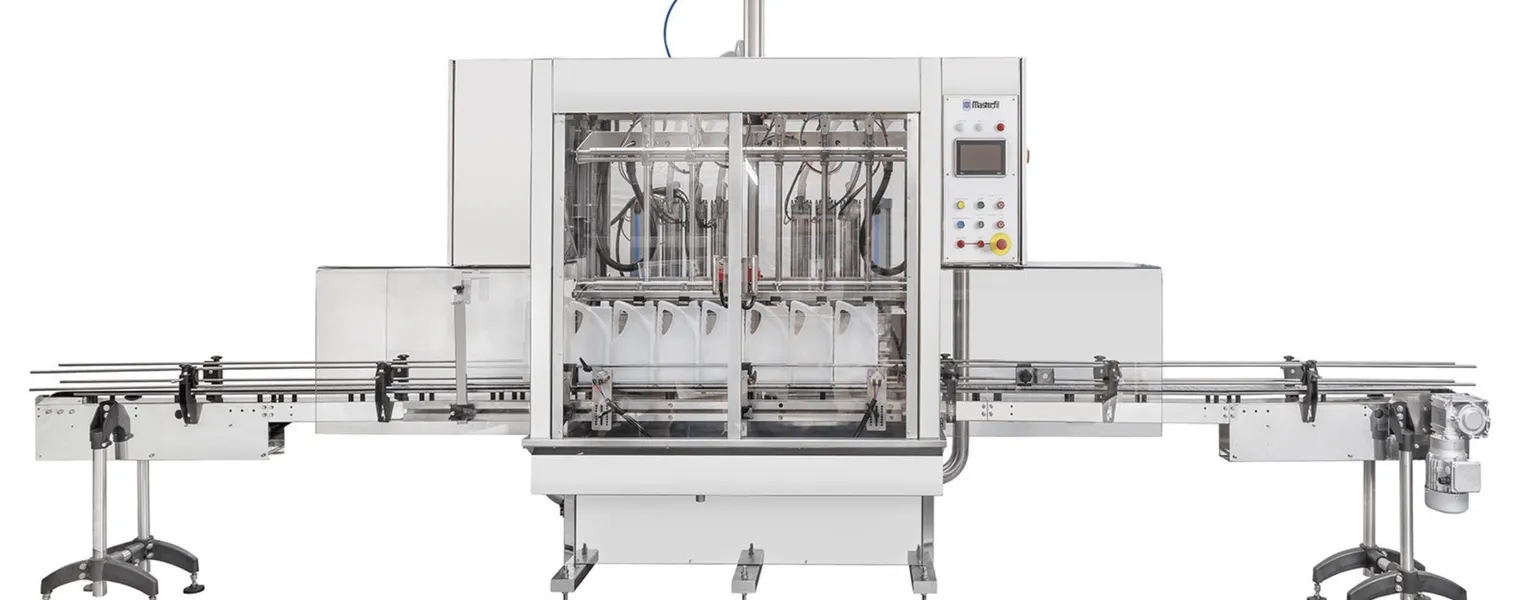
Supplier News
AdBlue is a registered trademark for a diesel exhaust fluid (DEF), used in modern diesel vehicles equipped with selective catalytic reduction (SCR) technology. SCR is an emission control technology that reduces nitrogen oxide (NOx) emissions from diesel engines.
In the SCR process, AdBlue is injected into the exhaust gases before they enter the catalytic converter. The heat from the exhaust causes AdBlue to break down into ammonia and carbon dioxide. When the exhaust gases pass through the catalytic converter, the ammonia reacts with the nitrogen oxides, converting them into nitrogen and water vapour – harmless substances that are released into the atmosphere.
Using AdBlue in diesel vehicles equipped with SCR systems helps to meet stringent emissions standards by reducing NOx emissions, which are a major contributor to air pollution. Many modern diesel cars, trucks, buses, and other commercial vehicles use AdBlue to comply with environmental regulations.
AdBlue presents specific challenges in its manufacturing and filling processes
To ensure your product's quality, efficiency, and regulatory compliance, the team at Adelphi Masterfil have compiled their guidance, in response to the top 5 challenges reported by customers. Read on to find out more…
1. Contamination control
AdBlue is highly susceptible to contamination. Even the smallest impurities can compromise its effectiveness. Robust filtration systems with protocols for handling and storage are essential, with an emphasis on regular cleaning of your filling equipment and storage tanks.
How is this best achieved?
If your filling machine doesn’t already utilise Clean-in-Place (CIP) functionality, we advise speaking with your equipment supplier, since it reduces the manual aspect of machine cleaning. In terms of frequency of cleaning, this can be determined by carrying out a Risk Assessment, taking into account factors such as the type of product being manufactured, the complexity of the equipment, and the potential for product carryover.
2. Storage and temperature management
AdBlue is particularly sensitive to temperature extremes, leading to crystallization in cold temperatures and decomposition in heat. Insulated storage tanks in climate controlled storage facilities prevent degradation and ensure greater longevity.
How can I control the temperature of my storage vessels?
Water Jacketed Vessels are equipped with a double-walled structure, with the outer layer containing circulating water. The water acts as a highly efficient heat exchange medium, absorbing or releasing thermal energy as needed to regulate the temperature of the product inside the vessel. The water jacket provides a consistent and uniform temperature distribution, preventing localized hot or cold spots that could compromise the quality and integrity of stored products.
3. Quality assurance
Ensuring the purity and quality of AdBlue is paramount at every stage of manufacturing process, with regular testing, adherence to ISO standards and certifications confirming product compliance.
How can my supplier assist my QA process?
When you work for an ISO certified business, working with suppliers who also adhere to ISO standards is essential. They will have a more thorough understanding of your internal processes, and it fosters a streamlined and integrated supply chain. This alignment in quality management systems promotes a shared understanding of processes, quality expectations, and continuous improvement initiatives. The standardized approach facilitates seamless communication, reduces the risk of errors or discrepancies, and enhances the overall efficiency of your operations.
4. Product waste & spillage prevention
Proper handling procedures are essential to eliminate environmental hazards and safety risks. Spillage is a significant risk to business in terms of the health and safety of employees, the costs associated with a clean-up operation, the interruption of production meaning reduced profitability potential, and more.
What practical solutions are recommended to mitigate these risks to my business?
It’s a common misconception that dripping and/or spillages represent the highest amount of product lost for your business. For example, dripping can spoil a pre-placed label, or prevent a downstream label application from being well achieved. Spillages can necessitate preventable expenditure in terms of clean-ups and production downtime.
Spill containment systems on filling machines significantly mitigate these risks. Ask your machinery supplier about the kinds of Drip Trays and Frame Trays which may be included in their products. The best examples are configured to contain and drain drips or spills into the base of the machine, from where the product can be recovered for recycling or safe disposal. Adelphi Masterfil has a great example – a swing-cup under the nozzle of their Boom Arm Filler, which collects drips.
The biggest loss of product is due to flushing, which is part of the cleaning process. Cleaning out one type of product at the end of a production cycle, ready to begin filling the next product. A machine trough gives the opportunity to recover product which would otherwise be lost, or to dispose of it safely. This is a very controlled process, also enabling machine cleaning chemicals to be disposed of in an environmentally friendly way.
5. Equipment maintenance
Regular cleaning, inspection and maintenance schedules for storage tanks and filling equipment are crucial. Preventative maintenance and automated monitoring systems for your equipment health give you the opportunity to rectify any potential issues before they become critical.
What is considered best practice when it comes to equipment and machine maintenance?
There are three types of maintenance:
- Reactive machine maintenance, also known as breakdown maintenance, is conducted in response to a breakdown.
- Corrective maintenance is the process of detecting an issue whilst performing another maintenance task on a machine, and arranging for the problem to be sorted when first spotted.
- Preventive maintenance includes routine procedures that are completed on a regular basis to catch and fix problems before they actually occur.
We always recommend preventative maintenance.
The cost of regular, planned maintenance is minimal when compared to the cost of a major breakdown, which could halt your operations entirely. We recommend a full service annually, in the same way that you would care for other critical equipment such as your car! In many instances, your supplier may be able to offer simple remote troubleshooting, and may even be able to login to your equipment programme remotely to enact corrections, so you should always reach out if you are unsure or beginning to get concerned.
Successfully managing these challenges in AdBlue manufacturing is best achieved as a continuous commitment to excellence between your business and your suppliers – where your shared goal is to maintain the integrity of AdBlue, contributing to cleaner emissions and sustainable transportation.
Cutting-edge filling technology for AdBlue
Key Features of Adelphi Masterfil's Semi-Automatic Filling Machine for AdBlue:
- 500ml to 25Litre volume range
- 1 or 2 pneumatically powered filling heads
- ±0.2% accuracy for cost-efficient production
- 316L stainless steel / PTFE / Viton contact parts
- Variable fill speeds can be used during the filling cycle
- Neck location to enable safe nozzle entry
- Nozzles rise whilst filling to reduce foaming
- Non-drip cut-off nozzle for clean filling
- Filling tray to contain spillages
- Flushing circuit for in-place cleaning
- Quick and easy to clean machine design
- High-quality construction using corrosion-resistant materials
Additional Features of Adelphi Masterfil's Fully Automatic Filling Machine:
- Up to 12 pneumatically powered filling heads
- ±0.15% accuracy with SERVO control upgrade
- PLC controlled, with recipe-driven HMI for machine settings
- Totally enclosed 304 stainless steel and PVC filling area
- Temperature monitoring to ensure product integrity
- Filling trough with sump pump option for product recovery
- Fully automatic container handling system includes ‘no container, no fill’ sensing
- Pneumatically operated bottle stopper for precision
- Stainless steel conveyor with variable speed control

Watch a video about Adelphi Masterfil filling machines for AdBlue using the links below:
Semi-Automatic Filling Machinery for AdBlue >>>
Automatic Filling Machinery for AdBlue >>>
Read about the experience of UK AdBlue manufacturer Noxdown here >>>
This article was originally published by Adelphi Group of Companies.
Related News
-
Supplier News
Adelphi: Environmentally Preferable Purchasing – Key considerations for sustainably and ethically minded businesses
-
Supplier News
Adelphi Masterfil: Filling your low viscosity products – Top tips
-
Supplier News
Pharma Hygiene Products: Why automation? The benefits for the mixing process
-
Supplier News
Pharma Hygiene Products: Navigating the waves – Global trends in bulk shipping across key industries
-
Supplier News
Adelphi Healthcare Packaging: Pharmaceutical primary packaging – What is it?