Adelphi Healthcare Packaging: the impact of Annex 1 for pharmaceuticals
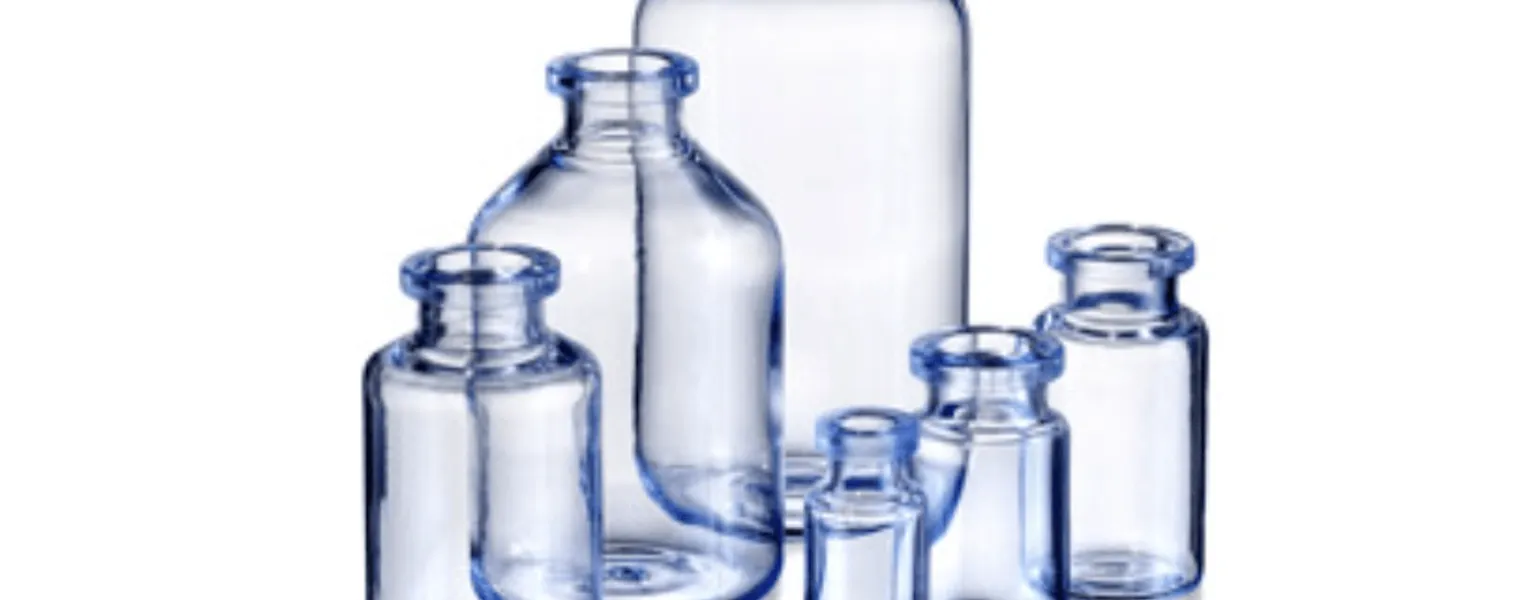
Supplier News
What Is Annex 1?
Annex 1 is a Good Manufacturing Practice (GMP) regulation submitted in 1971 designed to provide both guidance and certification for manufacturers to produce goods in safe and sterile environments. This regulation refers to the manufacture of sterile products, cleanroom classification, monitoring and personnel gowning. Annex 1 is also used to support the manufacture of other goods where the reduction of contamination is considered necessary.
In August 2023, Annex 1 was revised and resubmitted to be in line with new ISO regulations and procedures. This sparked wide debate across the industry on how it would influence future procedures, and the financial impact on smaller scale projects. Despite this, there are areas that leave space for interpretation. After its last revision in 2008, it’s fair to say that the several new changes to Annex 1 will have a significant impact on how sterile products are produced. Overall, Annex 1 is there to provide manufacturers with the necessary validation and certification to demonstrate that procedural protocol has been followed and is in line with industry expectations. In this article we discuss how Annex 1 will affect pharmaceutical manufacturers in future how your choice of primary packaging could help ease the journey to compliance.
How does Annex 1 affect the pharmaceutical industry?
Although Annex 1’s change has been widely debated, it has comes at a pivotal time for the pharmaceuticals and biotech industries. With technological advancement in medicine ever evolving and new sectors such as biotech and nuclear medicine continuing to grow, the latest Annex 1 updates provide much needed guidance and obligatory safety procedures to both serve and protect pharmaceutical companies and patients.
- Media Fill: Otherwise known as Aseptic Process Simulation (APS); this is where a liquid composed of specific chemicals is used to fill all sides and areas of a sterile container and then sealed within. This is then incubated and inspected over a period to see whether a product is contaminated during aseptic procedure. Annex 1 has now made this procedure mandatory not just for liquid-based products but also for non-filtered formulations, sterile powders, and lyophilized (freeze dried products).
- Cleanrooms: (particulates): Annex 1 will now mandate cleanroom particles are monitored down to between 5.0 - 0.5 micrometers.
- Barrier technologies: This includes machines such as isolators, filtered vacuums and restricted-access barrier systems which will now be required to provide suitable protection for housing stable Grade A environments.
- Disinfection: Annex 1 has made it compulsory to both document and frequently clean post and pre-production to achieve an above satisfactory level of contamination control. This process will need to be monitored and later validated within regulation to achieve full compliance with the new regulation.
With the above updates, more rigorous procedures must be followed, resulting in a potential need for investment in new equipment which smaller drug companies may struggle to finance. This may lead to a need to outsource certain processes in order to ensure compliance with GMP Annex 1 and ISO11737 regulations.
Mitigating the impact of Annex 1
The new regulations have presented a challenge for smaller scale projects. Ever more thorough procedures, additional personnel, and investment in adequate machinery could be seen as insurmountable obstacles, however there are solutions to ease the way to compliance.
Ready to Use primary packaging components provide peace of mind in adhering to the Annex I guidance. Vials and stoppers can be supplied sterile and ready-to-use in an aseptic environment. This offers a cost-effective alternative to sterilising your packaging in-house. RTU vials and stoppers are supplied with full sterility certification, conforming to industry wide regulations and are a great solution for projects where resources don’t allow for inhouse sterilisation. An example of Sterile RTU vials is the SCHOTT adaptiQ® range which is supplied in a choice of secondary packaging formats, clean, sterile and pyrogen free. AdaptiQ® sterile vials can be processed manually, or on a range of new and existing fill-and-finish lines. Rubber stoppers too can be supplied sterile and ready-to-use for incorporation into your aseptic manufacturing process, with examples including West’s NovaPure Rubber Stopper.
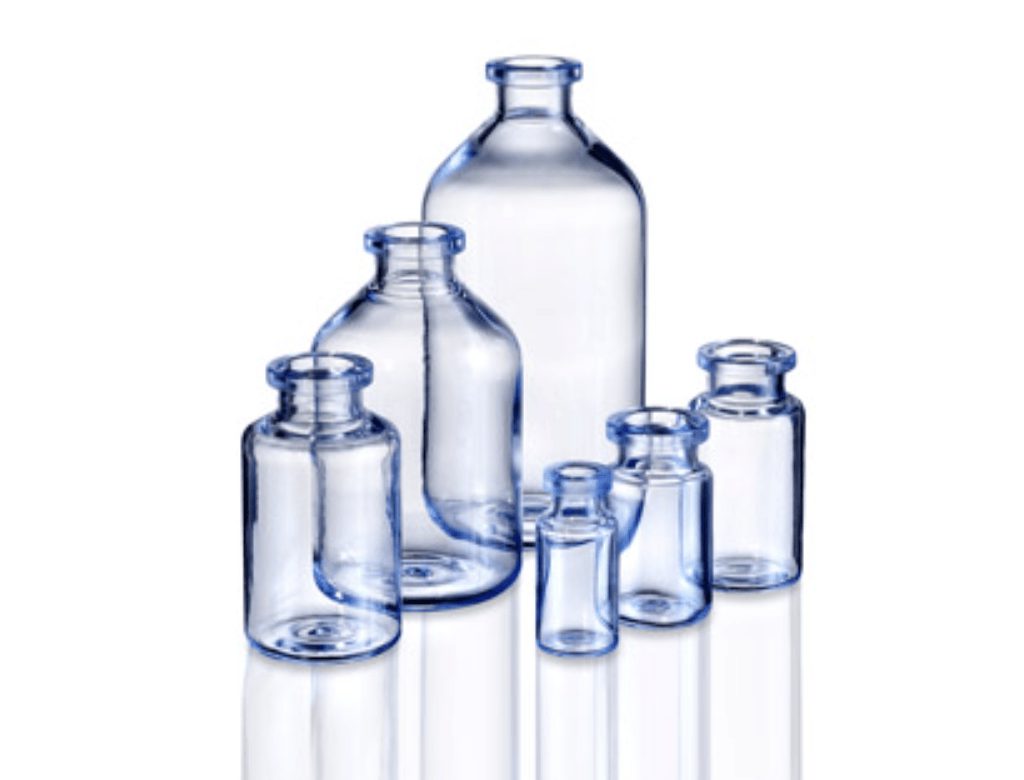
For more information on SCHOTT adaptiQ® vials or West’s NovaPure Rubber Stoppers, please get in contact with our team, and we can provide globally trusted technical advice and support.
Conclusion on why the Annex 1 revisions are overall a good measure despite its impact on the pharmaceutical industry
In conclusion, Annex 1's recent revisions reflect the evolving landscape of the pharmaceutical industry, emphasizing safety and sterility in an era of increased manufacturer accountability. While these changes may present challenges, alternatives like sterile RTU vials offer practical solutions for pharmaceutical research projects, reducing financial burdens and ensuring compliance with the updated regulations.
If you want to know more about sterile packaging, browse our sterile packaging range and discover our full offering of RTU packaging.
This article was originally published by Adelphi Healthcare Packaging.
Related News
-
Supplier News
Adelphi: Environmentally Preferable Purchasing – Key considerations for sustainably and ethically minded businesses
-
Supplier News
Adelphi Masterfil: Filling your low viscosity products – Top tips
-
Supplier News
Pharma Hygiene Products: Why automation? The benefits for the mixing process
-
Supplier News
Pharma Hygiene Products: Navigating the waves – Global trends in bulk shipping across key industries
-
Supplier News
Adelphi Healthcare Packaging: Pharmaceutical primary packaging – What is it?