5 top tips for scaling up formulation and mixing: from laboratory to large-scale batches
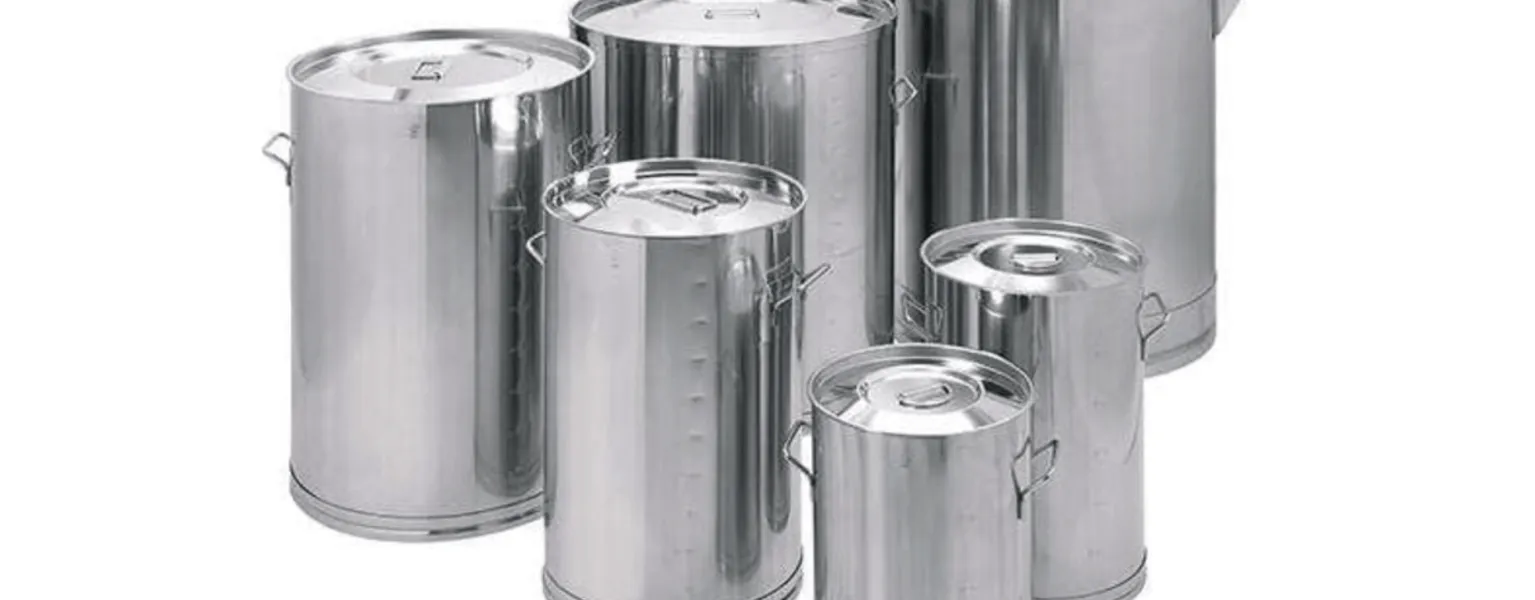
Supplier News
In product development, transitioning from small laboratory-scale batches to commercially viable production is a significant milestone. This transformation presents many challenges, but far more opportunities! To help you achieve a seamless and efficient scale-up process, industry expert Dean Willis – with over 30 years of production experience – shares his 5 Top Tips for success.
1. Ensure precise formulation and documentation
Begin by meticulously documenting your laboratory-scale formula. Ensure that you understand the interactions between ingredients, and how they affect the final product. Consistent and detailed documentation is vital as it will be your roadmap during scale-up.
Formulation changes, even minor ones, can have a cascading effect. For example, an error of 1g in a 1L batch size becomes a far more serious potential error of 100g in a 100L batch. By keeping detailed records, you can make adjustments as needed to maintain precise product consistency.
2. Conduct thorough feasibility studies
Before scaling up, Dean advises that businesses of all sizes perform comprehensive feasibility studies. This involves evaluating the suitability of your process, equipment, and raw materials for large-scale production. Identify potential bottlenecks, quality control measures, and safety considerations. This proactive approach helps prevent potentially costly surprises, to ensure a smoother transition throughout the scale-up process..
3. Choose the right equipment
Selecting the appropriate mixing vessels and equipment is paramount, as laboratory-scale equipment may not be robust enough for larger batches. Factors to consider include vessel capacity, mixing mechanisms, and safety features. Quality equipment not only ensures smooth production, but also minimises wear and tear; reducing downtime and maintenance costs.
Collaborating with a trusted equipment supplier who is experienced in scaling-up processes – such as Pharma Hygiene Products, who bring over 75 years of industry expertise – is invaluable. High quality equipment ensures greater efficiency and consistency in your production. Pharma Hygiene Products provide trusted guidance based upon your specific needs and can demonstrate their proven record of success using case studies and customer testimonials.
4. Fine-tune your mixing process
The mixing process plays a pivotal role in product quality. Factors such as mixing speed, time, and order of ingredient addition must be optimised for large-scale batches. Use your laboratory-scale data to create a mixing protocol that can be scaled up effectively. This means that your customers will always have a great experience of your product. Inconsistent mixing could mean that some batches are different thicknesses or lumpy, which could stop your customers from repeat purchasing.
Experiment and adjust as needed to achieve the desired product attributes consistently.
5. Rigorous quality control
Maintaining high levels of quality control throughout your scale-up process is vital. Implement comprehensive quality control measures, including real-time monitoring and testing. Track variables such as viscosity, temperature, pH, and particle size distribution. Regularly calibrate your instruments and involve experienced chemists to interpret the data. Be prepared to make adjustments, to ensure your final product meets the same quality standards as the lab-scale version, when produced to a commercial scale.
Read a Case Study: Nelsons Spatone utilise their 2,500L mixing vessel from Pharma Hygiene Products to maintain the temperature of their large product batches whilst mixing. Increased demand for their ‘Spatone’ range of liquid food supplement sachets meant that their existing vessel could no longer keep up, and this presented an opportunity for Nelsons to streamline their processes.
To see examples of mixing vessels in-action, please use the links below:
Pharma Hygiene Products Product Video
Scaling up your formulation and mixing is a multifaceted process that requires precision, planning, and attention to detail. By following these 5 Top Tips, you can navigate these challenges and make the transition from laboratory-scale batches to commercially viable products efficiently and effectively. Above all, remember that making use of collaboration with industry experts can be your most valuable resource in the scale-up journey.
This article was originally published by Pharma Hygiene Products - part of the Adelphi Group of Companies.
Related News
-
Supplier News
Adelphi: Environmentally Preferable Purchasing – Key considerations for sustainably and ethically minded businesses
-
Supplier News
Adelphi Masterfil: Filling your low viscosity products – Top tips
-
Supplier News
Pharma Hygiene Products: Why automation? The benefits for the mixing process
-
Supplier News
Pharma Hygiene Products: Navigating the waves – Global trends in bulk shipping across key industries
-
Supplier News
Adelphi Healthcare Packaging: Pharmaceutical primary packaging – What is it?