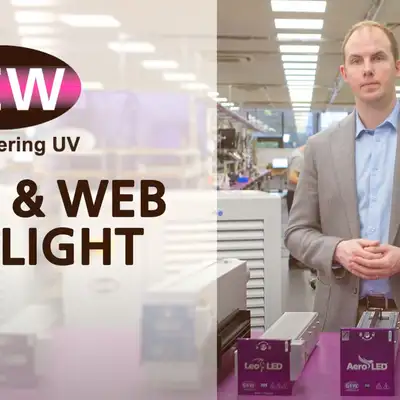
Discover the power of GEW UV LED curing for label & web printing
In this latest video demonstration, Robert Rae, GEW’s Managing Director of Sales, and Jennifer...
GEW designs and manufactures Arc and UV LED curing systems for printing, coating and converting applications. The company is the leading manufacturer of UV systems for label and narrow web printing and is experiencing a growing global presence in sheetfed and web offset for commercial printing and packaging.
GEW's UV systems are available for all new machinery, and can be retrofitted to any active press, allowing printers to breathe new life into older printing equipment. GEW has a world-class production facility at its UK headquarters, subsidiaries in the USA & Germany, and an extensive list of worldwide distributors.
UV cured packaging is produced via the process of package converting in many shapes, sizes, and constructions and is either rigid or flexible. Rigid packaging is made from paper, corrugated, cardboard, and carton board that is printed, varnished, and converted into various shapes. Flexible packaging is constructed using single- or multi-layer plastic and metal films that are front or reverse printed, laminated, and converted into forms that are sealed with heat and/or pressure.
Packaging converters and consumer packaged goods (CPG) companies rely on a mix of UV printing and UV coating technologies to deliver aesthetically pleasing designs that promote and protect the package's internal contents, develop innovative functionality tailored to specific markets and preferred portion sizes, differentiate products, and facilitate sustainability efforts. Examples of UV curable application technologies utilised by packaging converters include gravure, flexo, offset, digital inkjet, and other types of web and sheetfed coaters all of which can be equipped with GEW's mercury arc, UV LED, and hybrid designs that enable operators to quickly swap between arc and LED curing systems.
Product labels communicate information such as ingredients, proper use and handling, and safety warnings. They clearly identify brand names, trademarks, and logos; provide decoration; grab the attention of potential consumers; offer chances to win a prize, encourage buyers to make a purchase, and even provide instructions on how to properly dispose or recycle the item or packaging when finished.
In central impression (CI) printing, narrow, mid, and more often wide web materials are evenly and securely supported via a large centrally located cylinder with separate flexo print stations delivering graphics, text, varnishes, and coatings one transfer at a time via anilox cylinders and flexible photopolymer plates.
While CI presses can be solvent-based, water-based, or UV, newer UV LED curing technology offers more compact lamphead housings and significantly reduced heat transfer to substrates, constructions, and machine components; both of which significantly expand the potential of UV curing for flexible packaging jobs run on CI presses.
Sheetfed corrugated and folding carton or carton board are typically direct flexo printed using water-based inks that are dried with infrared and followed by an inline end of press or offline UV coater. Glossy UV varnishes give packaged box goods an attractive look while also protecting printed text and graphics during converting, filling, shipping, and handling. Corrugated and folding carton represents the largest printed packaging category and is used to promote, protect, contain, and dispense all the numerous consumer and industrial goods that are supplied in rigid paper carton and box board packaging.
Alternatively, corrugated and folding carton can be direct printed using UV digital inkjet and offset while lithographic lamination, litho lam for short, is a printing and converting process in which web or sheetfed UV offset printed paper is UV coated and laminated to corrugated substrates which are then die-cut, folded, and glued into rigid boxes.
In label converting, manufactures around the world rely on UV cured inks, coatings, and adhesives to create highly decorative, durable, and functional product labels that exhibit significantly brighter and bolder colours than water- or solvent-borne formulations. Labels are often film laminated with a UV curable adhesive, further protected with a UV curable matte or gloss varnish, and ultimately applied to a wide range of consumer and industrial goods and packaging. When brand managers want products to stand-out from the competition, they insist on UV cured labels.
To produce the extensive range of label types, converters utilise multiple print technologies designed for narrow and mid-web processes including flexo, digital inkjet, offset, letterpress, and screen; all of which can be equipped with GEW's mercury arc, UV LED and hybrid lamp designs that enable operators to quickly swap between arc and LED curing technologies.
Many commercial printers are increasingly repositioning themselves as multi-channel print providers. While focused primarily on media, marketing, and print used in business transactions, natural extensions are the printing of other promotional items, pressure-sensitive labels, and entry-level packaging that does not require much specialty equipment or post-print converting.
To deliver high-quality and single sourcing of such diverse print products, commercial printers around the world rely on a range of technologies including offset, flexo, letterpress, digital inkjet, gravure, and screen; all of which can be equipped with GEW's mercury arc, UV LED, and hybrid lamp designs that enable operators to quickly swap between arc and LED technologies.
UV curable direct-to-product decoration is used to transform the plain, blank canvas of many manufactured items into visually appealing surfaces that display single or full colour graphics and designs; clearly identify brand names, trademarks, logos, and internal contents; promote and celebrate organizations and events; and provide text and symbolic guidance for use, care, and disposal.
Unlike labels and appliques which are generated in separate manufacturing processes and then physically applied to the exterior of finished goods, many decorating processes print directly onto an item's surface. For more demanding applications that require greater chemical resistance and/or longer life, pre-printed and UV cured films and foils, as well as thermoformed UV printed plastic sheets, are seamlessly injection moulded directly into part structures.
Product decorators rely on a mix of UV printing and coating technologies to fulfil a wide range of decorating and performance needs including pad, screen, digital inkjet, dry offset, offset metal decorating, and indirect flexo, all of which can be equipped with GEW's mercury arc, UV LED, and hybrid lamp designs that provide the ability to quickly swap between arc and LED curing technologies.